In recent years, we have seen major innovations in the field of medicine that have made a difference. 3D printing and the continuous advances related to this technology offer the medical industry a great deal of design freedom, adaptability and functional integration. In addition, this technology allows practitioners to gain full control over patient-specific materials, shapes and designs.
3D printing opens the door to customized solutions with a patient-specific approach. For example, with additive manufacturing it is possible to fabricate prostheses or dental implants from patients’ anatomical data.
Benefits of 3D printing in the medical field
3D printing has revolutionized many sectors, and the medical industry has been no exception. This innovative technology has led to numerous advances such as the personalization of devices and prostheses or the manufacture of drugs.
Some of the benefits this technology provides to the medical industry are as follows:
- Accurate anatomical models: 3D printing has facilitated the creation of accurate anatomical models for the planning of surgeries and medical procedures. This allows physicians to study the patient’s anatomy in detail without the need for surgery. Therefore, we can say that thanks to additive manufacturing, medical procedures have become safer and more effective processes and, above all, have experienced a considerable risk reduction.
- Drug research and development: another breakthrough in 3D printing has been the manufacture of personalized drugs. This is an important improvement, especially for those who suffer from rare diseases and need a specific or personalized dose that is tailored to their needs.
- Cost and time reduction: one of the great advantages of using 3D printing in the medical industry is the possibility of reducing manufacturing time and costs. In this way, patients can obtain their devices, drugs or diagnostics much faster, which is an essential factor in this sector.
- Intelligent materials: although this research is still at a very early stage, there is the possibility of creating prostheses with materials that adapt to environmental conditions such as humidity, temperature…
Ultimately, all this results in a very important advantage in the medical field: a satisfactory user experience. Not only can the patient see the prosthesis to be fitted thanks to the 3D model beforehand and how it fits into his or her body, but he or she also gets a much faster and more efficient manufacturing process.
How to use 3D printing to replace a plaster cast
At Proto&Go! we are sponsors of the new podcast Toque de Ingenio, presented by Edgar Guerrero, Co-Founder of i-mas. Episode 8 is visited by Jordi Tura, CEO of Xkelet, a company that automatically designs a personalized immobilization in less than 5 minutes with a cell phone.
In this episode you will find out all about their 3D printed upper limb immobilization system, designed to replace traditional systems such as plaster casts and therefore solve the problems associated with them.
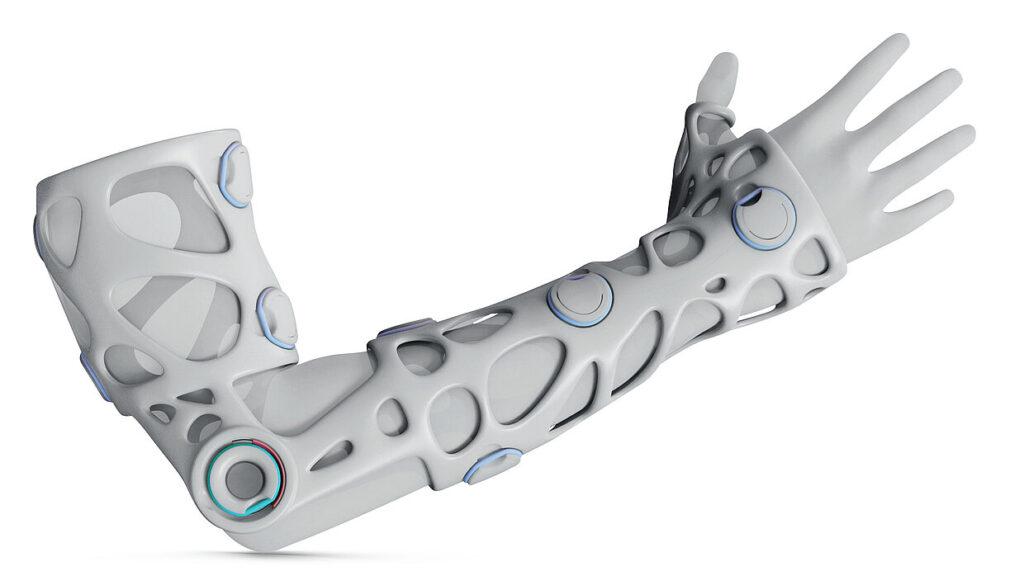
This innovative project brings numerous advantages for the medical industry and, above all, for patients. Its main advantage is the convenience of the process and the reduction of the risks associated with traditional methods such as plaster (such as infections, placement problems, etc.).
Want to know more? Listen to episode 8 of Toque de Ingenio in full!