Vacuum Casting
Ideal for the production of prototypes and short series.
Request your quotation with a CAD file to obtain
the quotation of your parts
Parts manufactured and delivered in just 10 working days
Customized and uncomplicated plastic parts
What does
the
vacuum casting process involve?
Vacuum casting(also known as urethane casting or silicone moulding) is a manufacturing method that uses silicone moulds to produce plastic parts in a relatively simple way and without the high costs and high lead times required for steel or aluminium moulds.
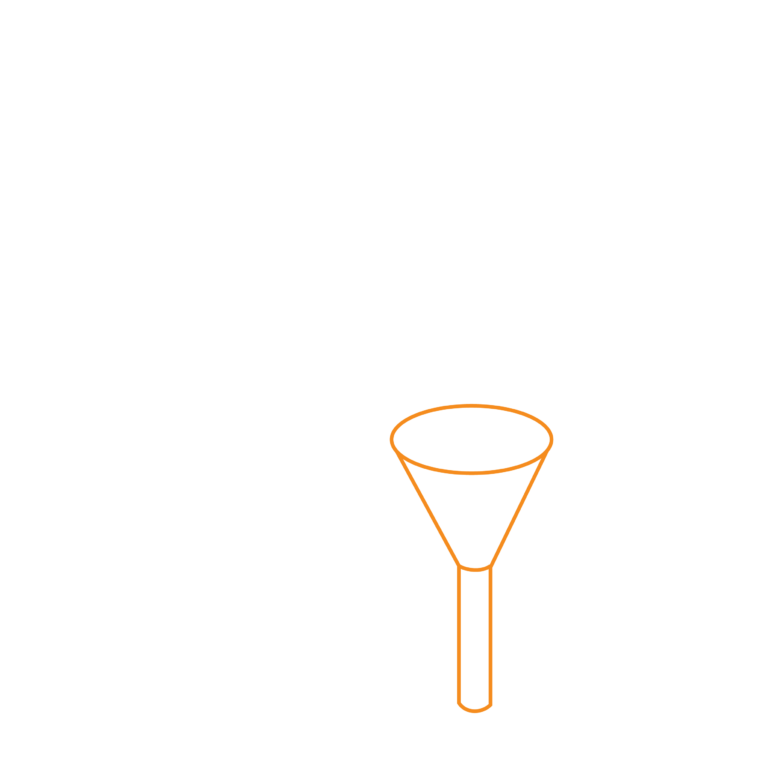
MANUFACTURING PROCESSES
Advantages of vacuum
casting
Scalability
Our vacuum casting process is optimal for low production volumes of between one single unit and several hundred parts. On average, each silicone mould can guarantee to cast around 20 parts. The maximum quantity will vary depending on the part design.
Durability
Polyurethane casting can be achieved with both rigid and flexible plastics. Polyurethane parts are generally as resistant or more resistant than injection moulded parts, and are significantly more durable than 3D printed parts.
Versatility
We offer a wide range of polyurethanes, both soft and flexible - such as Silicone, TPA, NBR... and rigid and resistant - such as ABS or PC. In addition, both opaque and transparent parts can be achieved.
Colours
Vacuum casting makes it possible to obtain pigmented parts according to a specific RAL or Pantone code. Therefore, the liquid polyurethane is coloured before casting. As a result, a colouring equivalent to that of an injection-moulded part is achieved.
Agility
The parts produced by vacuum casting are shipped within a period of 10 working days, depending on the requirements and quantity of the parts. On the other hand, when producing the same parts by injection moulding, a period of several weeks is to be expected.
Pieces with excellent finishes at reduced costs
Applications
Low Production Levels
Polyurethane (PU) parts produced by vacuum moulding are perfect for low-volume production – when quantities do not justify the investment in expensive injection moulds. As well as for the first series parts that can be produced weeks before the injection mould is ready.
Market testing
Thanks to the polyurethane casting process and the associated cost-effective tooling, it is simple and cost-effective to achieve a design and part quality approaching production levels. This method is suitable for the prototyping of elastomeric parts similar to silicone, TPA and NBR, and with hardnesses ranging from Shore A 30 to Shore A 90.
Advanced prototyping
A high quality finish makes them ideal for consumer testing, user evaluation and concept models. In addition, it allows unlimited complexity, including internal corners without radii, unachievable with CNC machining, and designs with no demolding or uniform wall thickness that cannot be injection molded.
Finishes options
PIGMENTED
The pigmented finish, regardless of its matt, satin or glossy texture, is ideal for those parts that may suffer wear due to scratching, so the colour of the part is maintained. The pigment colour can be chosen from both RAL and PANTONE
It is important to note that pigmented colour has a certain colour tolerance,
painting
Painting is a process used to treat the surfaces of plastic and metallic materials. There are three painting options: matte, satin and glossy. This technique significantly improves the visual appearance of the project. It is possible to choose the desired color using the RAL or PANTONE color chart.
Transparent
The PU- Flexible Polyurethane and PU- Rigid Polyurethane materials offer the option of a transparent finish, which allows light to pass through the part, allowing the contents of the part to be seen. We can resemble the finishes offered by PMMA, PC or transparent silicone.
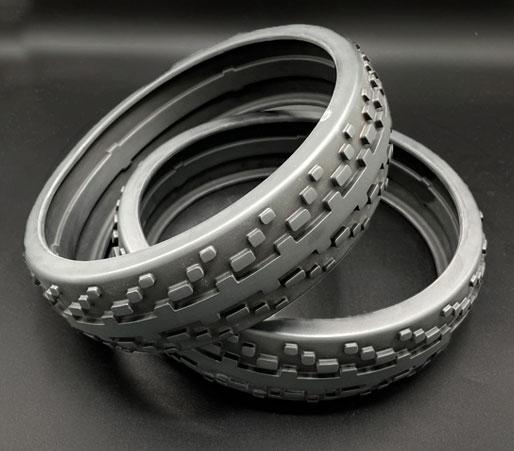
PU flexible
Highly versatile, it adapts to a wide variety of applications thanks to its flexibility, abrasion and impact resistance.
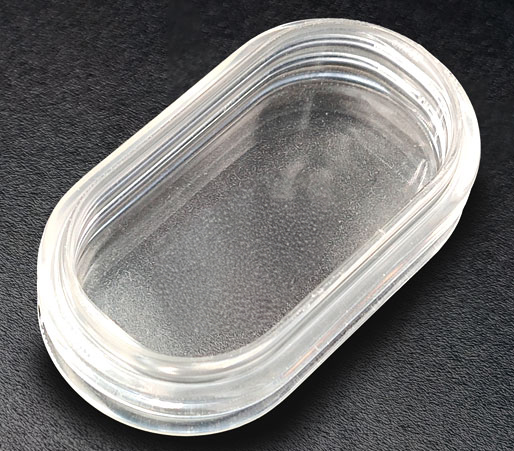
PU flexible transparent
It offers a wide variety of color and hardness options, making it ideal for the creation of customized products.
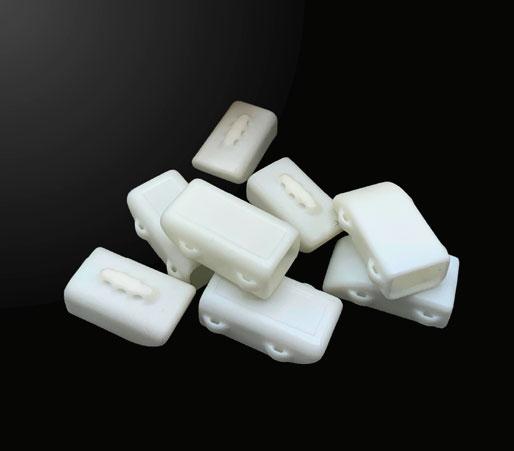
Pigmented rigid PU
Resistant and durable material characterized by its rigidity and dimensional stability. It has insulating properties.
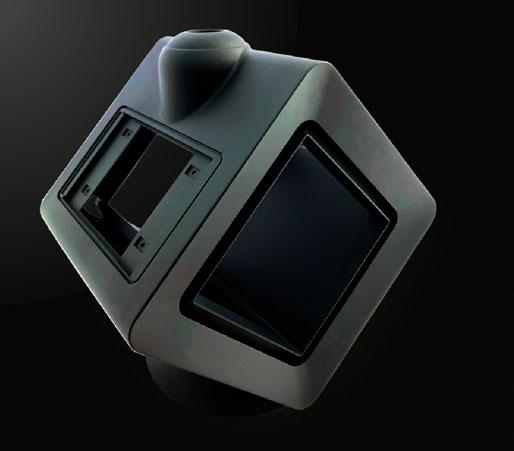
Painted rigid PU
Material that allows easy customization, thanks to its ability to be mixed with various additives and colorants.
Upload your CAD files to our platform, saving management and communication time by other means.
The 3D file is always essential for quoting and should only contain one part.
To indicate the threads present on a part you must upload a drawing in .pdf format and assign it to its corresponding part – 3D file.
To use our service it is no longer necessary to invest your time in making all the annotations on the drawings, the 3D file is enough
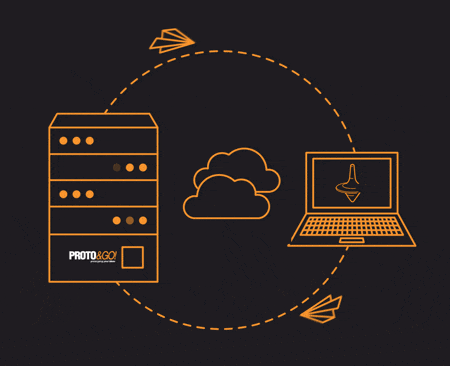