Guía de Diseño
- Impresión 3D -
PRINCIPIOS DE LA IMPRESIÓN 3D
Por impresión 3D se entienden los diferentes procedimientos a partir de los cuales se puede conseguir la construcción física de un diseño 3D mediante la técnica de fabricación aditiva.
A diferencia del mecanizado CNC, donde se obtiene la pieza a partir de la sustracción de material desde un bloque inicial, en la fabricación aditiva, se obtiene la geometría a partir de la solidificación capa a capa del material de partida.
Tradicionalmente esta técnica está más extendida y es más habitual para materiales plásticos, aunque el metal y otros materiales se abren paso poco a poco.
VENTAJAS DE LA IMPRESIÓN 3D
Rápidos plazos de entrega
Las piezas suelen enviarse en tan sólo 5 días, lo que permite acelerar las iteraciones de diseño y la velocidad de comercialización.
Geometrías complejas
Prácticamente se puede construir cualquier geometría, por muy compleja que sea sin las limitaciones de otros procesos de producción.
Coste
Al ser una tecnología de alta y fácil producción los costes para obtener piezas son generalmente más bajos que cualquier otra tecnología, siendo la elección ideal para prototipos previos y tests rápidos de producto.
Escalabilidad
Con la impresión 3D de Proto&Go! se puede fabricar una sola pieza o componente con la misma facilidad que docenas de piezas de producción sin necesidad de la inversión en utillajes o moldes.
Durabilidad
La impresión 3D puede ofrecer una gran resistencia al impacto, una flexibilidad media y una alta resistencia a los factores ambientales.
VENTAJAS DE LA IMPRESIÓN 3D
MJF – Multijet Fusion de HP
Es la última y más avanzada tecnología de impresión de grado industrial, y por ello es la escogida por Proto&Go! para la ejecución de sus proyectos.
Esta máquina ha sido desarrollada por la compañía HP para la obtención tanto de prototipos como de series de piezas en materiales como Nylon – PA12 o TPU flexible, entre otros.
Destacan la velocidad de fabricación y la resistencia de las piezas obtenidas, pudiendo obtener piezas 100% funcionales en pocos días y con una elevada resolución.
SLA – Estereolitografía
La estereolitografía pertenece a una familia de tecnologías de fabricación aditiva conocida como fotopolimerización, o comúnmente, impresión 3D de resina. Esta técnica utiliza como principio, la utilización de una fuente de luz (un láser) para curar resina líquida y transformarla en plástico endurecido.
Las piezas realizadas mediante SLA ofrecen la mayor resolución y precisión, los detalles más nítidos y el acabado de la superficie más liso de todas las tecnologías de impresión 3D, siendo ideal para piezas estéticas.
Por el contrario, tienen una desventaja y es que, al ser el material fotosensible, las piezas obtenidas no aguantan bien el paso del tiempo ni la exposición a la luz ambiental y generalmente son frágiles para secciones no muy elevadas.
Debido a ello, en Proto&Go!, se prefiere optar por el Mecanizado CNC de ABS para la obtención de piezas con objetivos estéticos como carcasas o carenados.
SLS – Selective Laser Sintering
Es una tecnología madura con la que obtener piezas en Nylon, Polipropileno u otros materiales a partir de la fusión de material en polvo mediante la aplicación de calor con un láser monopunto.
SLS es una tecnología previa a la MJF con características similares pero sin algunas de sus ventajas, como por ejemplo la isotropía del material y el tiempo de fabricación.
FDM – Modelado por Deposición Fundida
Esta técnica es considerada a menudo el método existente más sencillo. La tecnología de modelado por deposición fundida o FDM se basa en 3 elementos principales: una placa/cama de impresión en la que se imprime la pieza, una bobina de filamento que sirve como material de impresión y un extrusor. En resumen, el filamento es fundido por el extrusor de la impresora 3D, que deposita el material de forma precisa capa por capa sobre la cama de impresión.
Los materiales más habituales para este tipo de impresión, entre otros, son el ABS y el PLA.
La gran ventaja de esta técnica es su sencillez y economía, siendo por ello esta tecnología la que ha adoptado mayoritariamente el sector doméstico.
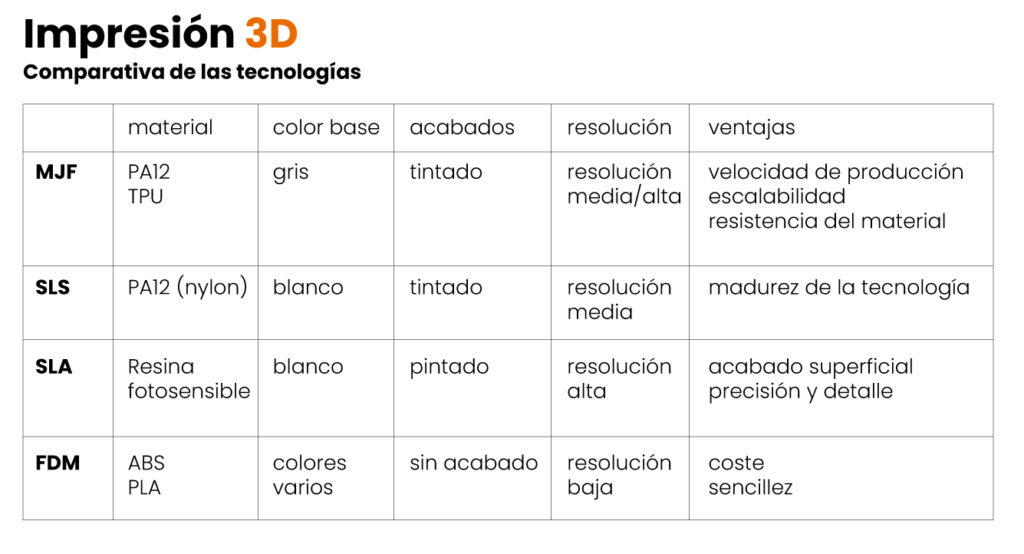
PROCESO - MULTIJET FUSION (MJF)
El proceso se inicia con un cabezal de recubrimiento que deposita una capa muy fina (normalmente 0,08 mm) del material en polvo, PA12 o TPU, en la plataforma de construcción. Tras la deposición de una primera capa, un segundo cabezal móvil aplica los agentes sobre la geometría de la pieza que delimitarán la zona que deberá ser sinterizada por un fusor que incorpora el propio cabezal.
Una vez escaneada toda la sección transversal, la plataforma de construcción desciende un grosor de capa en altura. El polvo no sinterizado permanece en su lugar para soportar las capas posteriores, eliminando la necesidad de estructuras de soporte.
El cabezal de recubrimiento deposita una nueva capa de polvo sobre la capa anterior, ya sinterizada, y el cabezal con los agentes y el fusor realiza una nueva pasada para sinterizar la nueva sección sobre las anteriores previamente solidificadas. Este proceso se repite hasta que todas las piezas están completamente fabricadas.
El resultado es un contenedor lleno de polvo y piezas solidificadas que se debe dejar enfriar al menos durante 24 horas antes de ser retiradas.
CARACTERÍSTICAS - MULTIJET FUSION (MJF)
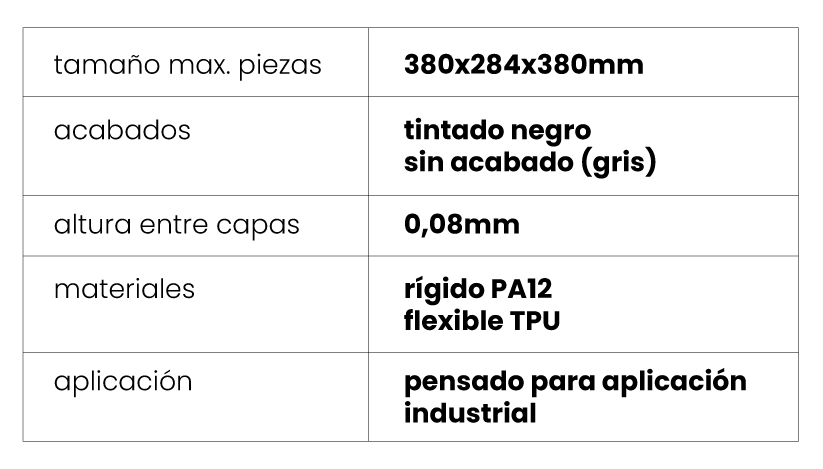
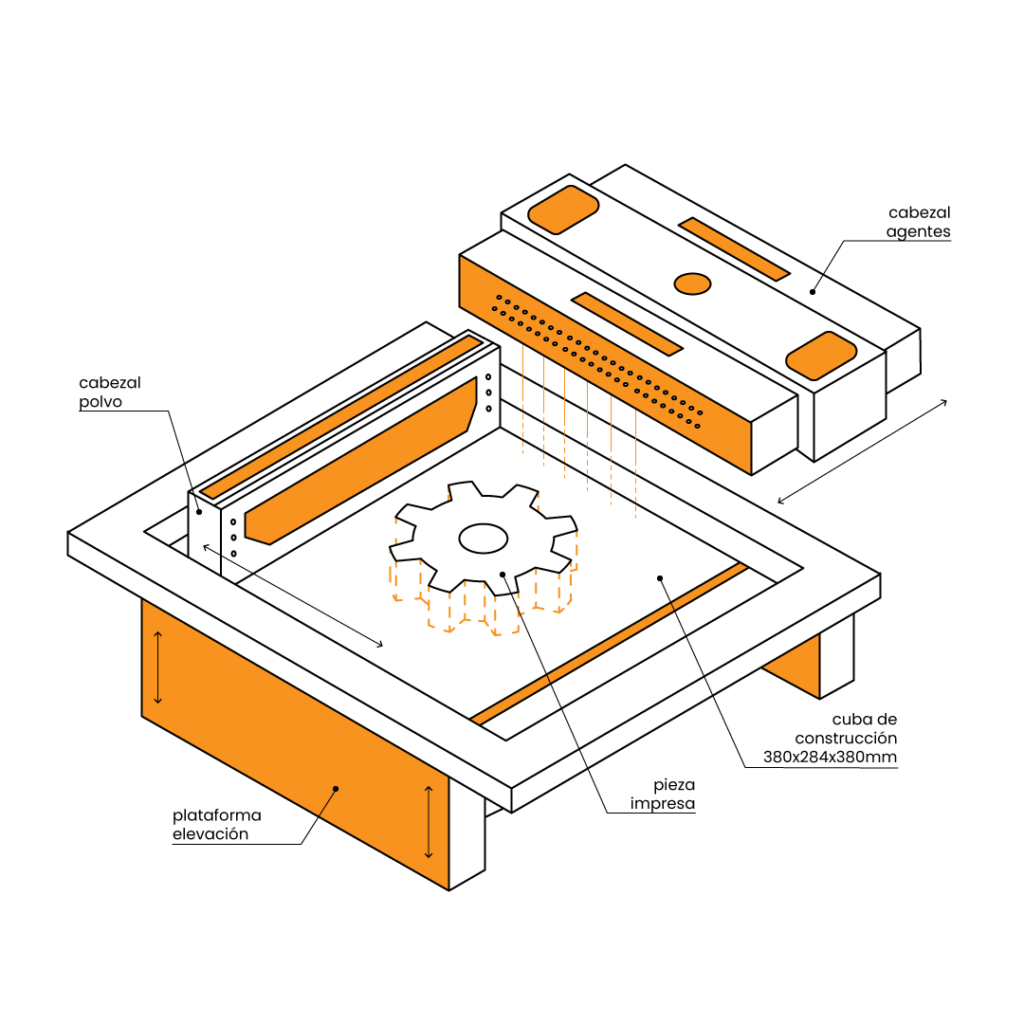
APLICACIONES - MULTIJET FUSION (MJF)
Las piezas obtenidas mediante la impresión con MultiJet Fusion se utilizan habitualmente a nivel industrial para la creación rápida tanto de prototipos como de producciones completas:
- aeroespacial
- automotriz
- productos de consumo
- productos industriales como maquinaria especial
- atención médica
Las piezas y prototipos funcionales MFJ se utilizan para:
- drones
- robótica
- maquinaria especial
- dispositivos ioT
- equipos deportivos
- calzado
- tecnología ortopédica
- educación
- dispositivos médicos
La impresión 3D mediante MultiJet Fusion (MJF) también es una buena tecnología para crear modelos arquitectónicos detallados a un coste razonable.
RECOMENDACIONES DE DISEÑO
La mayoría de los parámetros requeridos para la estrategia de impresión, como por ejemplo la posición y orientación de las piezas en la cuba entre otros, son definidos directamente por los técnicos de impresión 3D para optimizar los resultados, sin embargo, durante la fase de desarrollo de producto, los diseñadores e ingenieros pueden también tener consideraciones que aseguren la fabricabilidad de la pieza y con las que obtener piezas más económicas y sencillas de industrializar.
Hemos reunido algunas de las mejores prácticas para tenerlas en cuenta al diseñar una pieza y optimizar su coste.
DIMENSIONES
Característica
La impresora Multi Jet Fusion tiene una medida de cuba máxima de 380 x 284 x 380, por tanto ese es el tamaño máximo de pieza fabricable.
Regla de diseño
- Tamaño de pieza máximo fabricable: 380 x 284 x 380 mm.
- Tamaño de pieza mínimo fabricable: 3 x 3 x 3 mm.
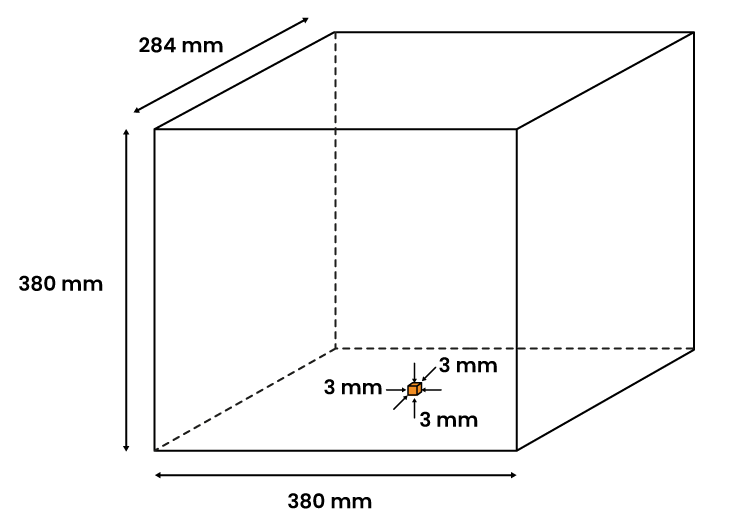
TOLERANCIAS
Característica
Como en cualquier proceso productivo, en la impresión 3D también existen unas tolerancias a tener en cuenta antes de plantear diseños de piezas que deban tener ajustes.
Regla de diseño
Tolerancia dimensional: ±0,3% de la medida nominal con un mínimo de ± 0,3 mm.
- Si la cota es menor de 100 mm. la tolerancia esperada es de ± 0,3 mm.
- Si la cota es mayor de 100 mm. la tolerancia esperada es de ± 0,3% de la cota original.
Ejemplos:
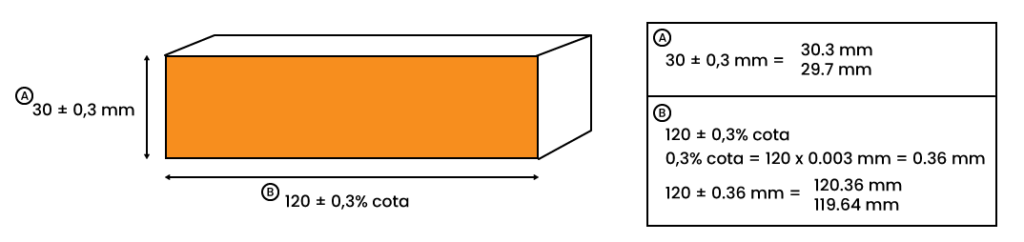
ESPESOR MÍNIMO
Característica
Las temperaturas elevadas que se generan en la sinterización del polvo pueden provocar deformaciones o roturas en las paredes demasiado delgadas. Por ello hay unos valores mínimos que no deben rebasarse para evitar defectos de construcción.
Regla de diseño
- Espesor mínimo fabricable: 0,5 mm.
- Espesor mínimo recomendado: 0,8 mm.
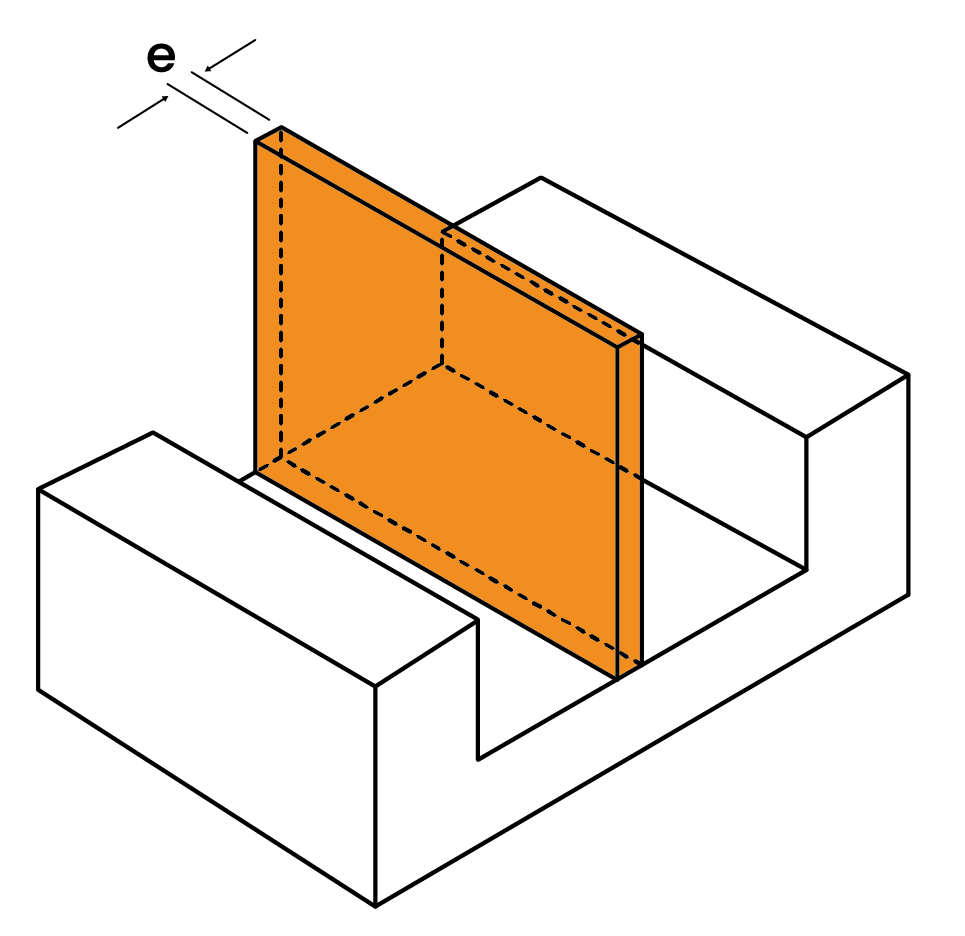
RECOMENDACIÓN
En caso de requerir paredes esbeltas (altas y finas) o con espesores pequeños, recomendamos el nerviado de la pared o la utilización de paredes auxiliares.
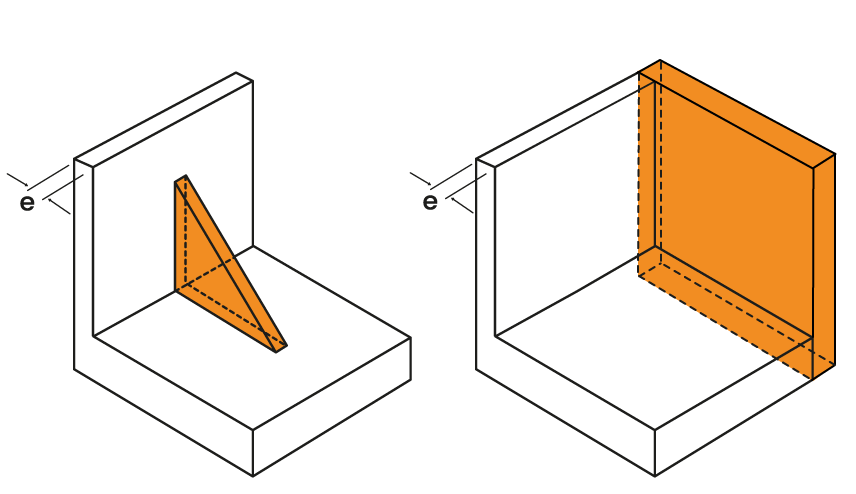
ESPESOR MÁXIMO
Característica
La fusión del polvo en grandes densidades de volumen no es posible debido a la concentración de temperaturas que se dan en el interior de la pieza. Además, en la impresión 3D el coste principal viene dado por la cantidad de polvo que contiene la pieza.
Por ambos motivos se recomienda evitar diseños con espesores de pared demasiado gruesos.
Regla del diseño
Espesor máximo recomendado:
- Para PA12 – 10 mm.
- Para TPU – 6 mm.
Nota:
En caso de requerir espesores superiores a los recomendados a la hora de imprimir la pieza, se realizará automáticamente con un “infill” (panel de abeja interior) con paredes de 3 mm de espesor y agujeros que permitan la salida del polvo alojado en el interior. También se puede optar por eliminar la pared completa y dejar a la vista el panel de abejas.
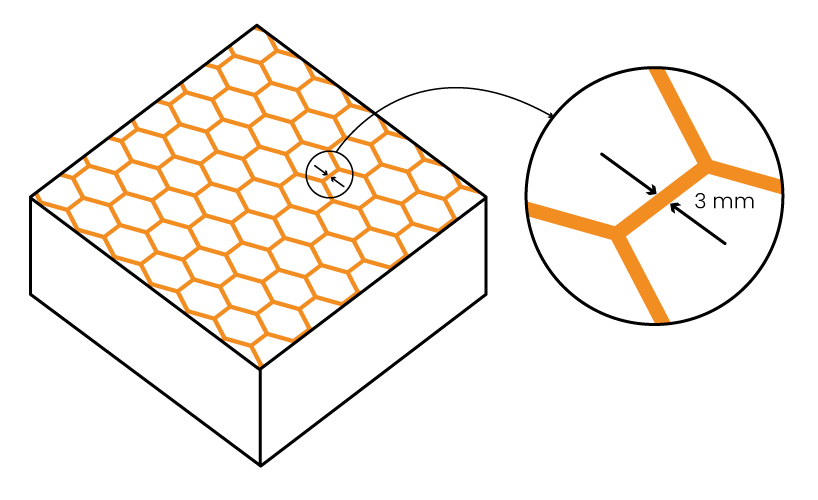
Recomendación
Realizar un diseño de pieza que incorpore elementos estructurales que rigidicen la pieza minimizando los espesores.
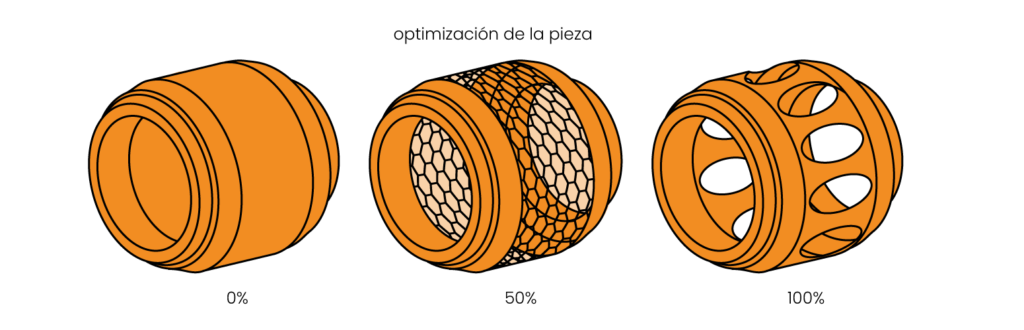
LETRAS O DIBUJOS
Característica
La tecnología Multi Jet Fusion permite imprimir letras y/o dibujos con una resolución y definición muy altas.
Regla del diseño
- Fuente mínima imprimible: 6 puntos
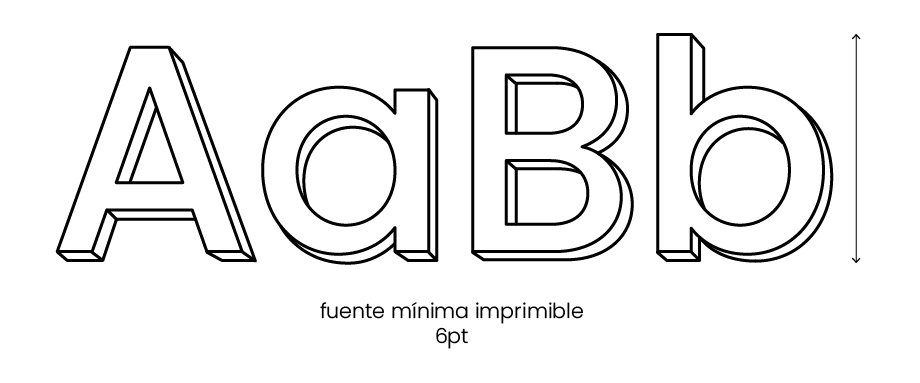
- Altura o profundidad mínima de letra: 1 mm.
- Anchura mínima de letra: 0,4 mm.
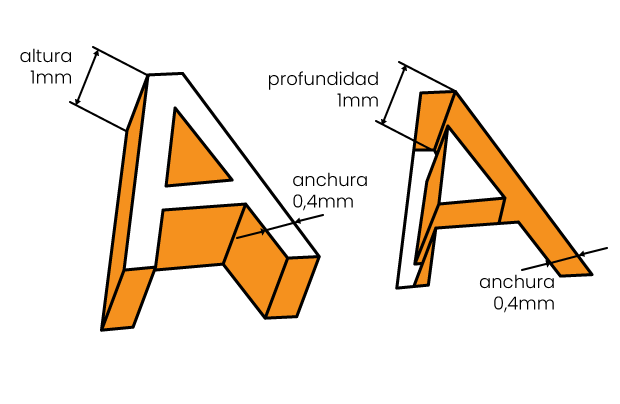
AGUJEROS
Regla del diseño
- Diámetro mínimo recomendado: 1,5 mm.
- Diámetro mínimo fabricable: 0,8 mm.
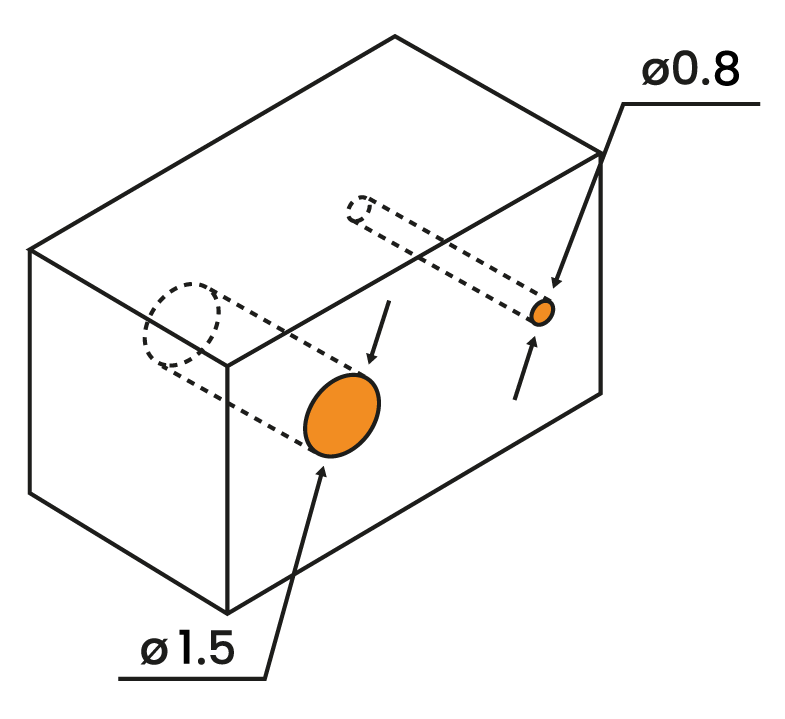
ROCAS/INSERTOS
Característica
Las roscas con diámetros superiores a M5 son imprimibles tanto en formato macho como hembra, siendo funcionales mediante la tecnología Multi Jet Fusion.
También es posible la colocación de insertos metálicos.
Recomendación
Para evitar problemas en el roscado se recomienda diseñar las roscas con una tolerancia de 0,2 mm. en diámetro.
De esta manera, si se pretende obtener un eje roscado de M6, cuyo diámetro exterior por normativa debería ser de Ø6, nuestra recomendación es reducir ese diámetro exterior a Ø5,8 para evitar problemas de tolerancias a la hora de roscar.
En el caso de un agujero roscado, tuerca o hembra, la tolerancia debe ser positiva, haciendo mayor el diámetro de lo que debería ser originalmente.
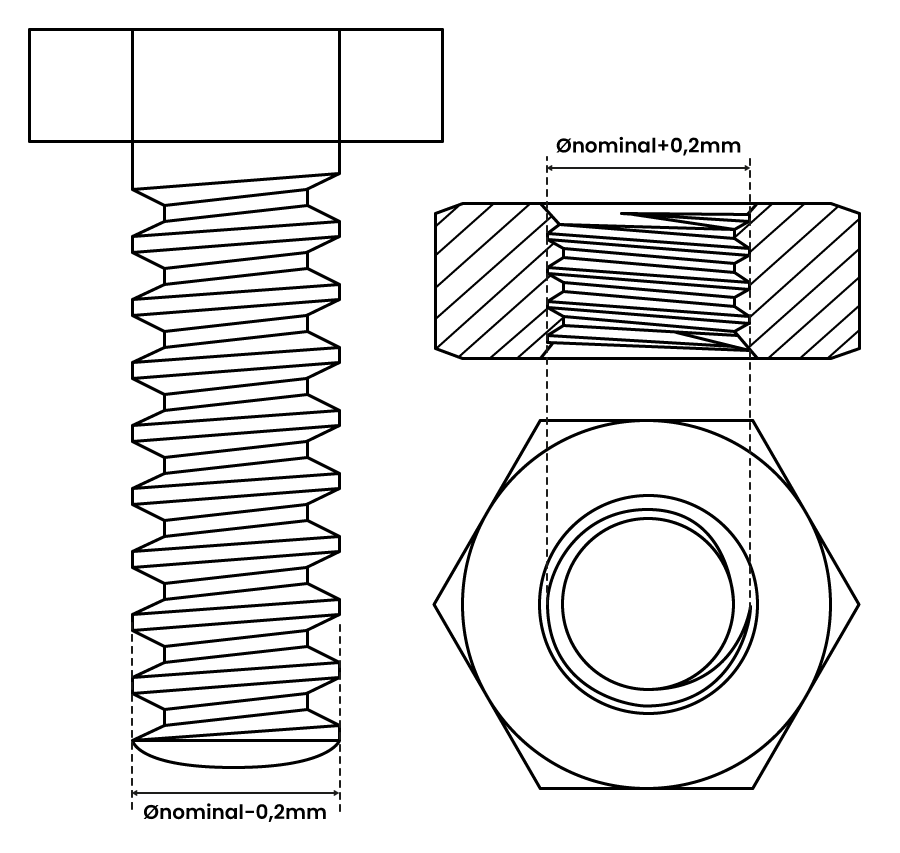
- Tornillo: Øexterior = Ønominal – 0,2 mm.
- Tuerca: Øinterior = Ønominal + 0,2 mm.
Nota:
Para roscas desde M3 a M8 los insertos metálicos son la mejor solución para la ejecución de roscas en una pieza impresa.
Si tiene preguntas adicionales, siempre puede ponerse en contacto con el departamento de Atención al Cliente de Proto&Go! en:
info@protoandgo.com | (+34) 932 20 71 04
o a través de nuestro sistema de chat online.