Guía de Diseño
- mecanizado CNC -
PRINCIPIOS DEL MECANIZADO CNC
El Mecanizado CNC (Control Numérico Computerizado) es uno de los métodos de fabricación y prototipado más utilizados, tanto para piezas metálicas como plásticas.
Esta tecnología de fabricación sustractiva, parte de un bloque de material en bruto al que se somete a un proceso de arranque de viruta mediante herramientas de corte que se suceden por fases hasta lograr la geometría final de la pieza deseada.
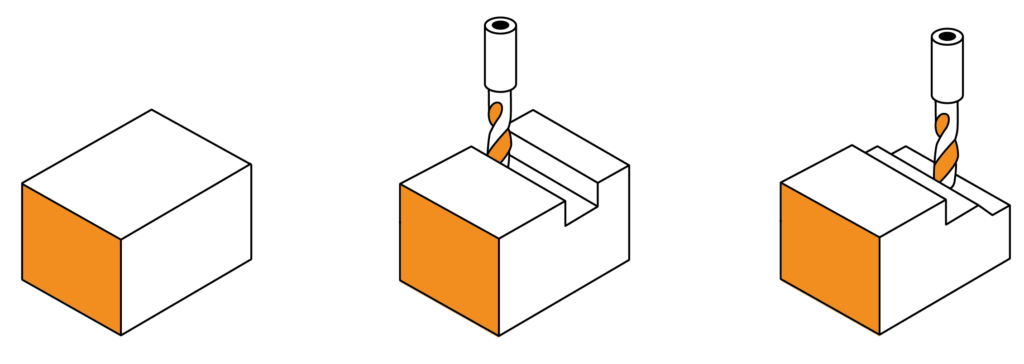
El mecanizado es la técnica con la que se pueden obtener las piezas de mayor calidad (comparada con Impresión 3D) y prácticamente se puede mecanizar cualquier tipo de material tanto metálico (entre otros, las aleaciones del aluminio, magnesio o aceros) como plástico (como ABS, Nylon, Delrin, etc…).
Pese a que muchas geometrías se pueden programar manualmente, desde Proto&Go! se solicita siempre un archivo CAD 3D para programar las máquinas CNC mediante software CAM, garantizando así la exactitud del resultado y evitando posibles errores de planos o de versiones.
PROCESO
Partiendo del archivo 3D, se procesa el archivo de la pieza a fabricar mediante un software CAM (fabricación asistida por ordenador) del que se obtienen las trayectorias de herramienta basadas en la geometría de la pieza a fabricar.
A partir de esas trayectorias virtuales obtenidas mediante el software CAM se genera un código máquina que indica al CNC de la máquina todos los parámetros y condiciones requeridos para fabricar la pieza: velocidad de giro de la herramienta, velocidad de avance del cabezal, profundidad de cada pasada, tipo de herramienta, etc.
En general, para la mayoría de las piezas, se requiere la intervención de diferentes herramientas, cada una con sus particularidades, que se suceden en diferentes fases de mecanizado hasta lograr la geometría definitiva.
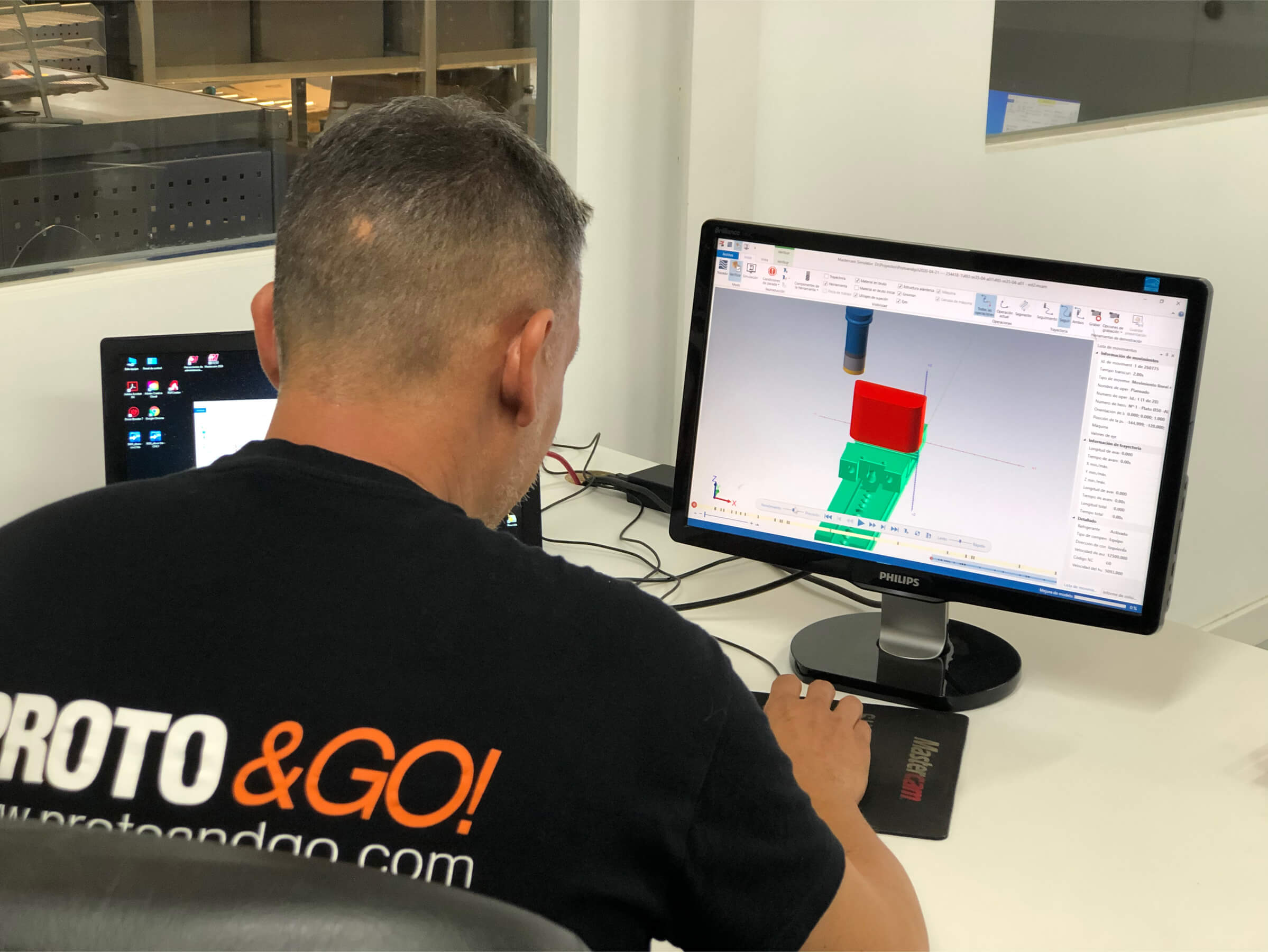
TIPOLOGÍA DE MAQUINARIA CNC
Entre otras características, la maquinaria de mecanizado se clasifica según la cantidad de ejes en los que pueden trabajar, siendo habitual hablar de 3, 4 ó 5 ejes.
Existe maquinaria con más ejes de trabajo u otras configuraciones, así como maquinaria dedicada al corte láser, corte por chorro de agua o electroerosión. Esta guía sin embargo restringe su alcance a la maquinaria CNC que trabaja por arranque de viruta mediante herramientas de corte.
FRESADO CNC - 3 EJES
Las máquinas CNC más habituales de 3 ejes incluyen tanto fresadoras CNC como tornos CNC.
Este tipo de maquinaria permite el desplazamiento de la herramienta de corte en tres ejes lineales, X, Y, Z (y/o interpolaciones entre ellos) relativos a la piez
En las fresadoras, el bloque de material es estático y son las herramientas las que rotan para conseguir velocidad de corte y poder arrancar material.
En el caso de una pieza fresada, la geometría resultante puede ser cualquiera, no debiendo limitarse sólo a piezas de revolución como sucede en el torno.
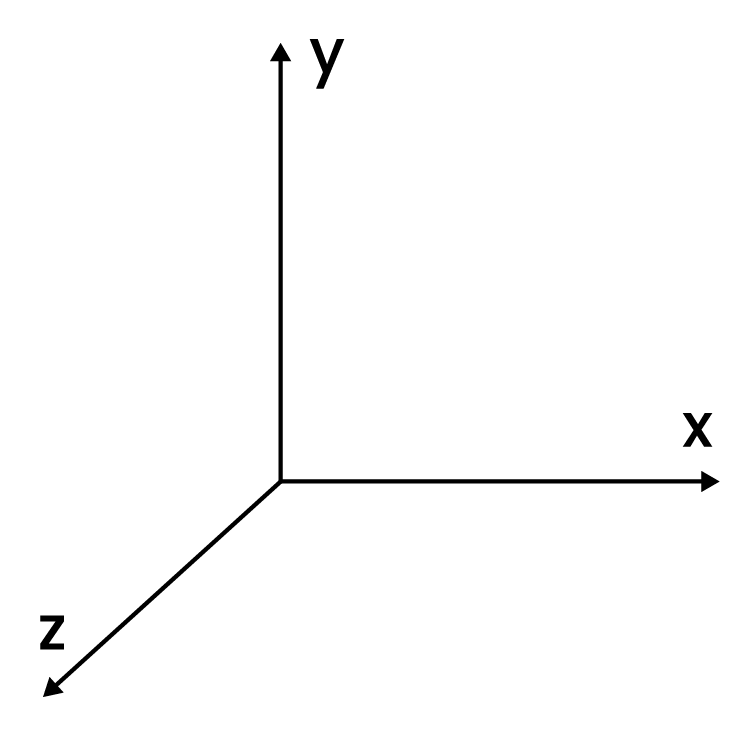
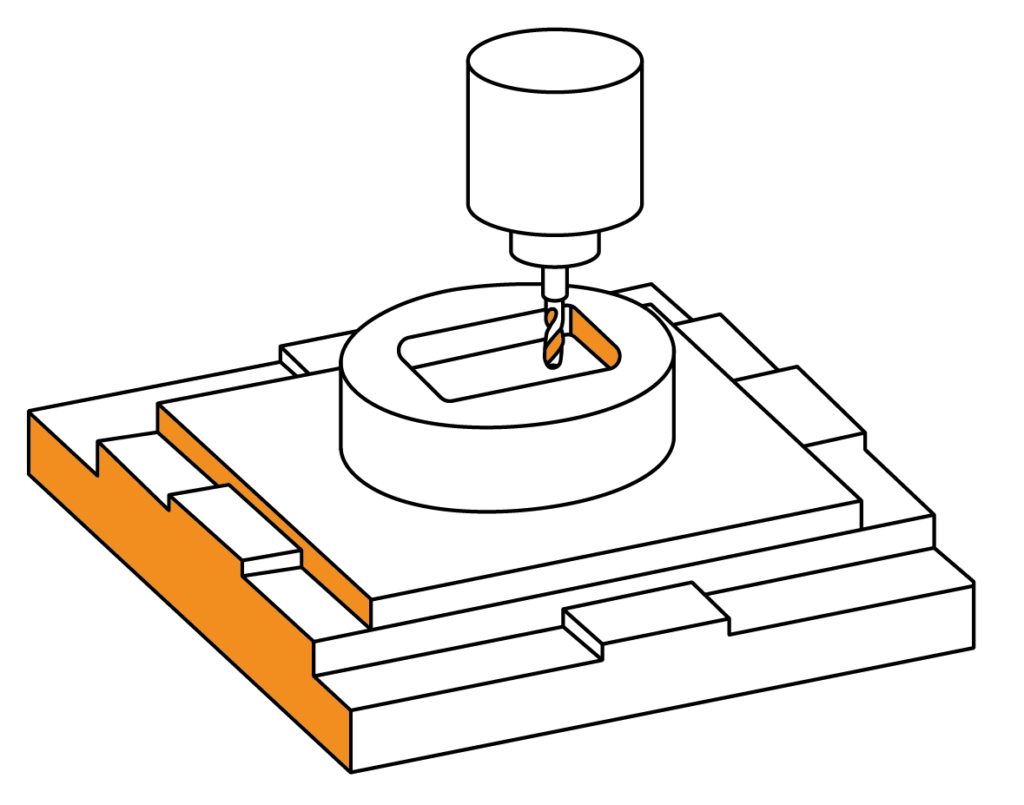
Los primeros 3 ejes permiten un movimiento relativo entre herramienta y material sobre un eje de coordenadas X, Y, Z.
Este es el tipo de fresadora más habitual y extendida.
FRESADO CNC - 4 ejes
Para dotar a la fresadora CNC de mayor versatilidad a la hora de posicionar una pieza respecto a su eje axial, se puede integrar un módulo electromecánico con un 4º eje que le concede un grado de rotación extra al centro de mecanizado.
Esta operación normalmente se realiza añadiendo este módulo de 4º eje a una máquina convencional de 3 ejes.
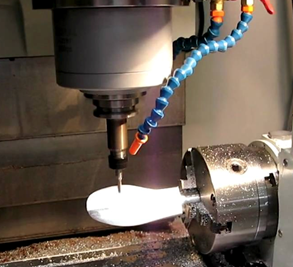
FRESADO CNC - 5 ejes
Los centros de mecanizado con 5 ejes, poseen bien una bancada motorizada o bien es el propio cabezal el que dispone de dos grados de libertad extra añadidos a los 3 ejes originales.
Generalmente las máquinas preparadas con 5 ejes son más versátiles en el proceso global de mecanizado pero su coste de adquisición es bastante más elevado por lo que las piezas procesadas en este tipo de máquina son generalmente más caras.
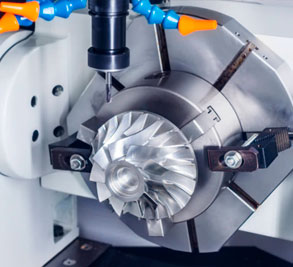
TORNEADO CNC - 3 ejes
La característica más evidente en el torno, es que el material en bruto rota sobre sí mismo en el cabezal y las herramientas inciden sobre él generando las trayectorias de arranque de viruta. El resultado es una pieza denominada “de revolución”.
Generalmente las piezas torneadas son más económicas que las piezas que requieren fresado puesto que el proceso es más ágil y sencillo de automatizar. Por ello, el torneado es un proceso con el que se pueden conseguir altas producciones con bajos coste, siempre y cuando se diseñe una pieza de revolución.
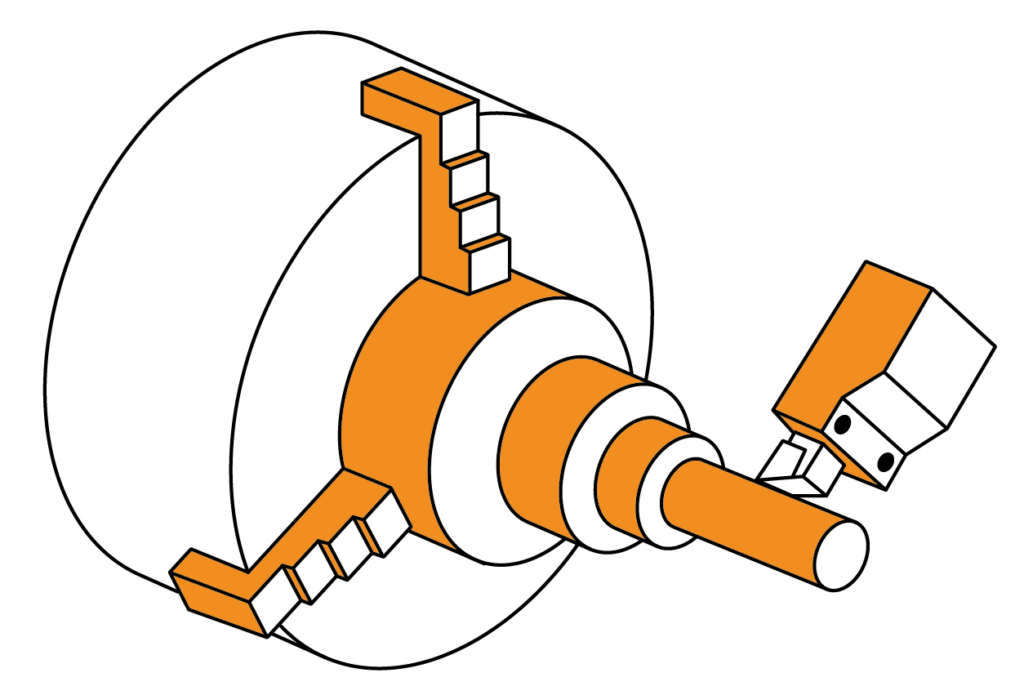
TORNEADO CNC - 4 ejes
La característica más evidente en el torno, es que el material en bruto rota sobre sí mismo en el cabezal y las herramientas inciden sobre él generando las trayectorias de arranque de viruta. El resultado es una pieza denominada “de revolución”.
Generalmente las piezas torneadas son más económicas que las piezas que requieren fresado puesto que el proceso es más ágil y sencillo de automatizar. Por ello, el torneado es un proceso con el que se pueden conseguir altas producciones con bajos coste, siempre y cuando se diseñe una pieza de revolución.
FABRICALIDAD
La mayoría de los parámetros, tales como la estrategia de mecanizado cnc, la velocidad de corte, el tipo de herramienta o la profundidad del corte, son definidos en taller, pero hay algunos detalles que se pueden realizar durante la fase de diseño de producto, no sólo para asegurar la fabricabilidad sino también para obtener piezas más económicas y sencillas de industrializar.
Hemos reunido algunas de las mejores prácticas para tenerlas en cuenta al diseñar una pieza y optimizar su coste .
ARISTAS INTERNAS
Característica
Las herramientas que se utilizan para mecanizar cajeras o rebajes interiores tienen forma cilíndrica por lo que no es posible obtener aristas de radio cero en los vaciados interiores.
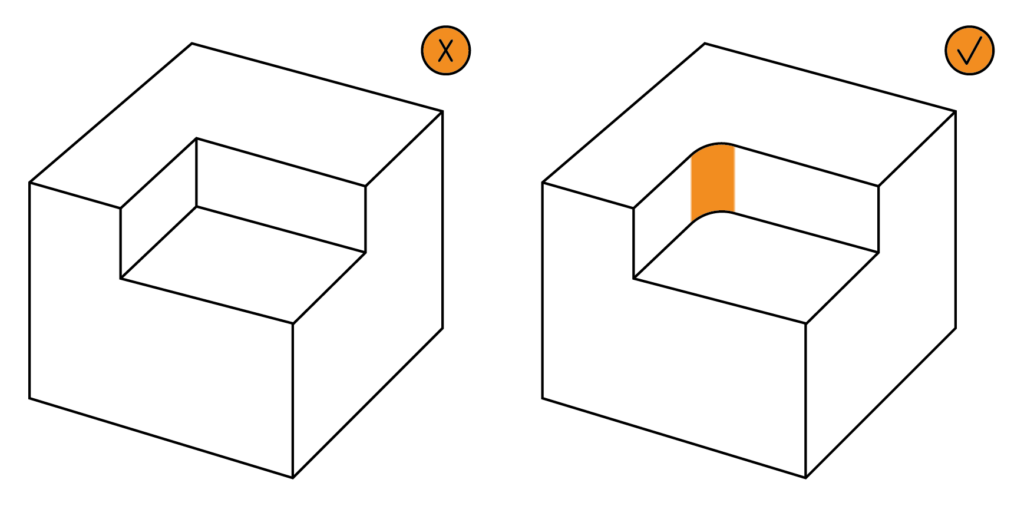
Regla de diseño
- El radio mínimo recomendado que se debe aplicar en una arista interna dependerá de la altura del propio vaciado, considerándose un valor razonable un radio mayor a 1/3 de la profundidad.
Cuanto mayor sea el radio aplicado mayor la facilidad de producir,
y por tanto, menor el coste.
- En cualquier caso, evitar radios inferiores a 1 mm.
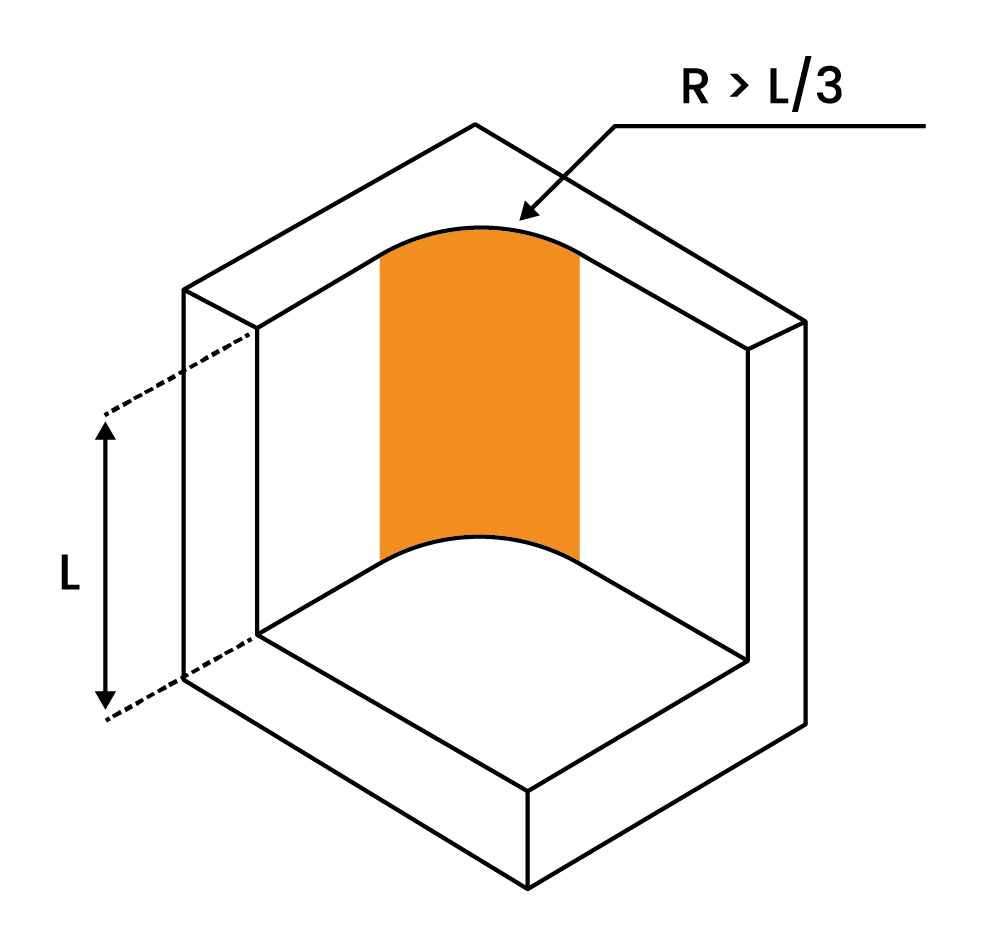
Recomendaciones
- En caso de que el vaciado interno deba alojar otra pieza cuyo ajuste pared con pared sea importante, se propone la opción de realizar salidas de herramienta en los radios interiores.
- Una solución alternativa e igual de óptima es la de realizar chaflanes exteriores en la pieza que se aloja en el interior de la cajera.
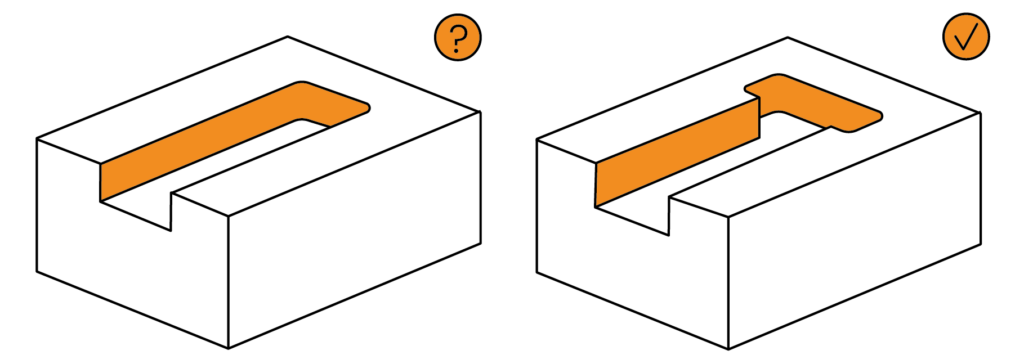
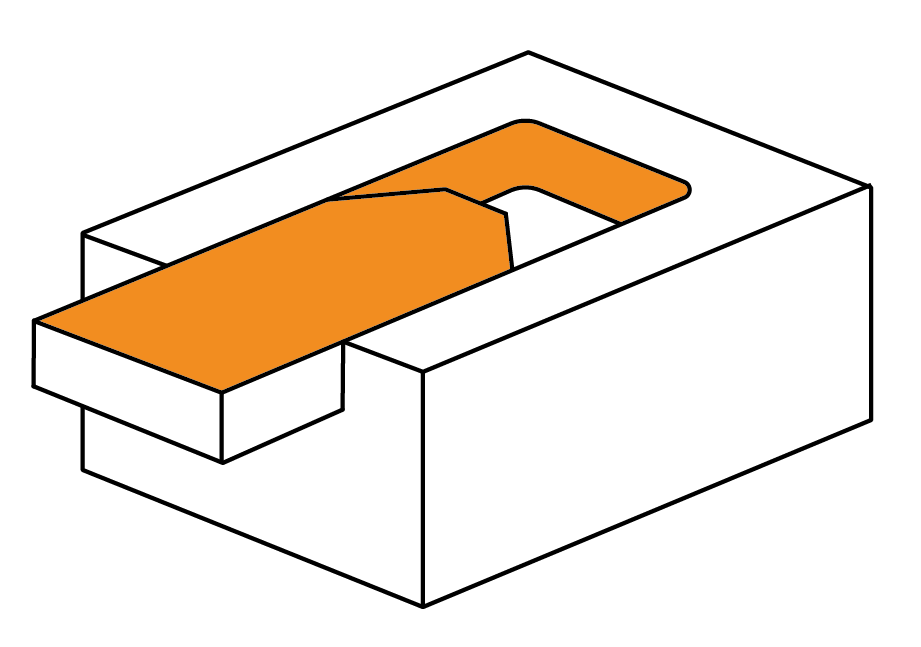
ROSCADOS
Característica
Regla de diseño
- La profundidad de roscado se define según el diámetro nominal de la rosca, siendo generalmente innecesario profundidades superiores a
3 x diámetro nominal de la rosca.
- Para poder realizar una rosca, el agujero debe estar dibujado en el archivo 3D y debe tener un diámetro equivalente al diámetro nominal de la rosca menos 1 vez el paso.
- El roscado de un taladro requiere un espacio libre de rosca al fondo del taladro, debiendo al menos ser este espacio de 3 veces el paso.
- Se recomienda diseñar taladros roscados a partir de M3 o superior.
- No es factible realizar roscas inferiores a M2.
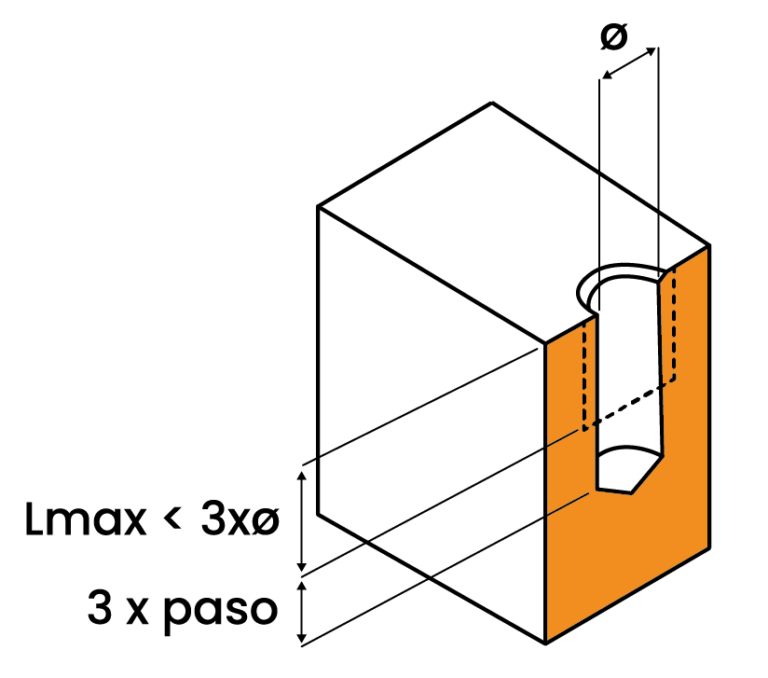
Recomendaciones
- No es recomendable realizar roscas profundas. Es más provechoso realizar el roscado en ambos extremos del taladro si se requiere usar la rosca por ambos extremos.
- Siempre que sea posible es más interesante, y económico, realizar los agujeros roscados pasantes en vez de ciegos.

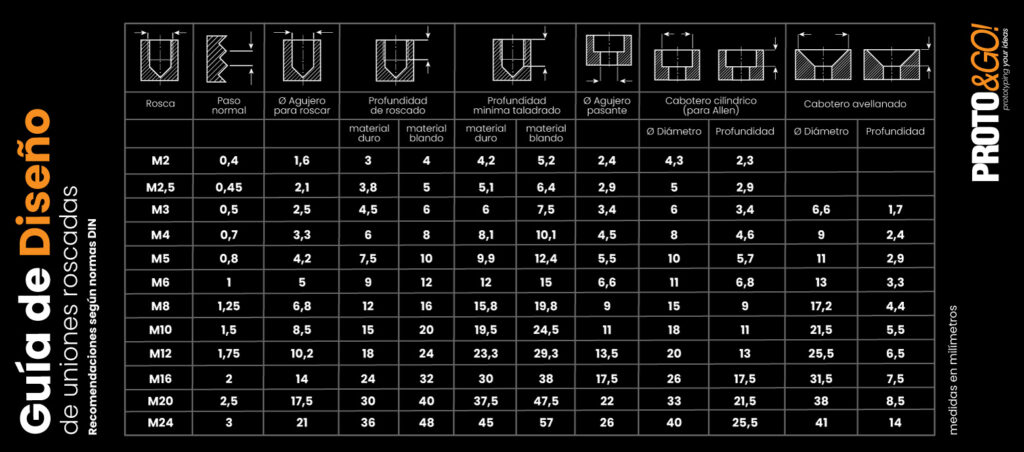
NEGATIVOS
Característica
Los negativos son secciones en el diseño donde geométricamente es imposible el acceso de una herramienta standard de mecanizado CNC.
Debido a la forma de las propias herramientas, generalmente cilíndricas, hay determinadas geometrías en las piezas diseñadas que pueden no ser alcanzables, generándose lo que se conoce como negativos (undercuts en inglés).
Hay algunas excepciones como las secciones de “T invertidas” para los que sí se dispone de herramientas, pero en general para poder fabricar un negativo se requieren o bien herramientas especiales fabricadas exprofeso, o bien procesos posteriores al mecanizado.
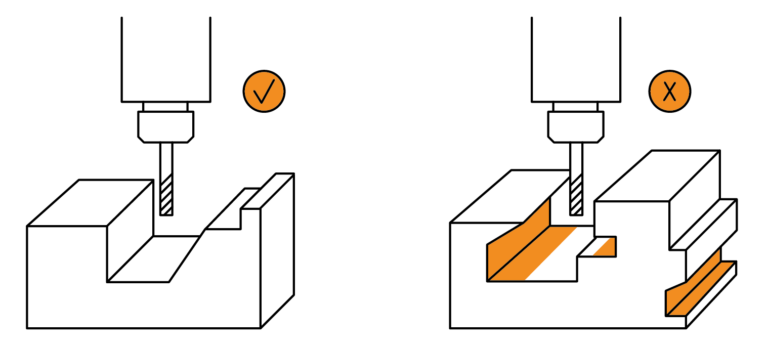
Regla del diseño
- Evitar la creación de negativos en el diseño de las piezas.
Recomendaciones
- Para evitar diseños con negativos se recomienda realizar el diseño requerido en dos piezas separadas posteriormente atornilladas.
TALADRADO
Característica
Regla del diseño
- Los taladros ciegos cuentan con un fondo cónico. A la hora de realizar el diseño hay que tener en cuenta este punto.
- Profundidad de taladrado recomendada: inferior a 4 x diámetro nominal.
- Máxima profundidad fabricable: 10 x diámetro nominal.
- Diámetro mínimo recomendado: Ø2,5.
- El diámetro mínimo fabricable es Ø0,5.
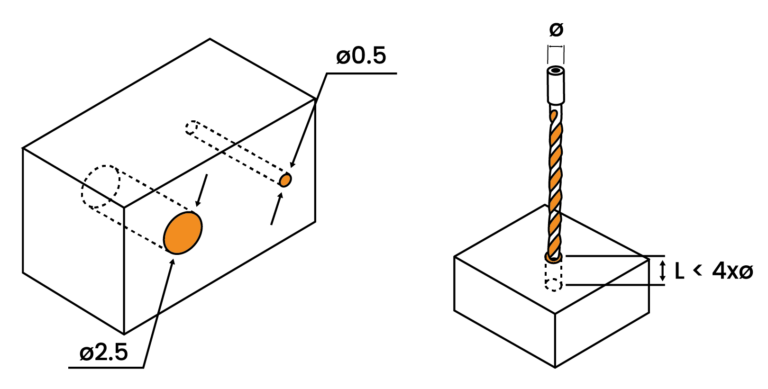
Recomendaciones
- Siempre que sea posible es más interesante realizar los agujeros pasantes en vez de ciegos.
- Se recomienda utilizar diámetros de taladrado standard ( Ø6, Ø7,5, Ø10,…) y se deben evitar medidas muy específicas que requieran herramientas hechas a medida ( Ø6,57)
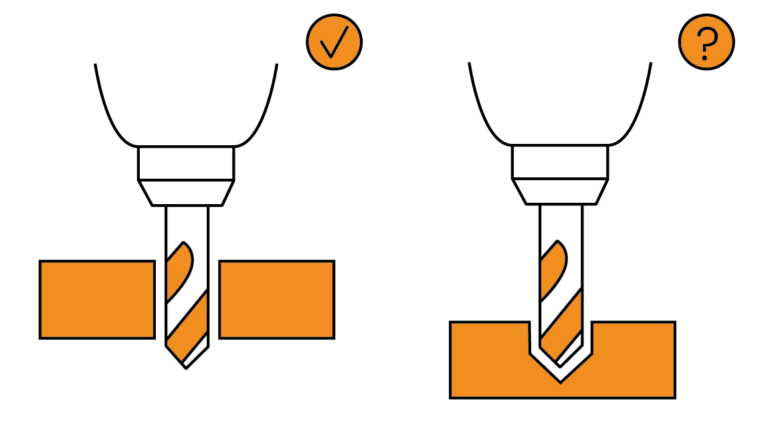
ESPESORES
Característica
Regla del diseño
- Espesores mínimos recomendados:
- Plástico: 1,5 mm.
- Metal: 0,8 mm.
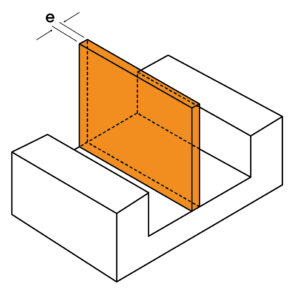
RANURAS
Característica
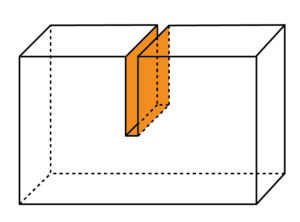
Regla de diseño
- Profundidad máxima:
- 15 x diámetro para plásticos.
- 10 x diámetro para aluminios.
- 5 x diámetro para aceros.
ENCOLADO / SOLDADO
Característica
Debido a las propiedades de determinados materiales, así como a la geometría requerida en algunos diseños cabe la opción de que para facilitar el proceso de fabricación y por tanto optimizar el coste, la construcción se deba realizar en varias partes posteriormente encoladas (plásticos) o soldadas (metales).
Este procedimiento se realiza habitualmente en el material plástico ABS debido a que gracias a sus propiedades se utiliza para la construcción de prototipos estéticos muy complejos.
Igualmente se puede proponer la utilización de una unión soldada en determinados diseños de piezas de aluminio que por su geometría no se puedan fabricar a partir de un único bloque.
Nota aclaratoria:
TOLERANCIAS
Tolerancias generales
La tolerancia es el rango aceptable para una dimensión, determinado por el diseñador y que garantiza el buen funcionamiento de la pieza en base a su forma, ajuste y función.
En caso de que la cotización no incluya un plano 2D con una solicitud de tolerancias específica, Proto&Go! fabricará las piezas, acorde a la norma ISO 2768fH para los metales y a la norma ISO 2768mK para los plásticos:
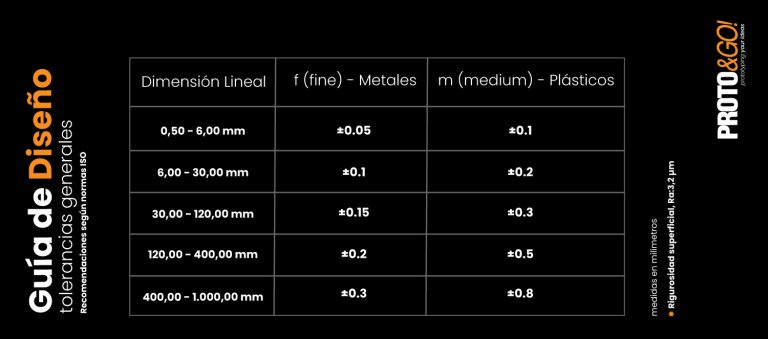
Tolerancias específicas
En el caso de que, por la funcionalidad de la pieza, las tolerancias generales no sean suficientes, el diseñador o ingeniero deberá indicar las tolerancias requeridas en un plano.
Es importante reseñar que cuanto más estrictas sean las tolerancias, mayor será el coste de fabricación de la pieza llegando incluso a doblar el coste que tendría la misma con unas tolerancias estándar.
Si existen tolerancias geométricas específicas o cualquier tipo de anotación que deba ser cumplida puede reflejarse en el plano adjunto también.
Para minimizar el coste de fabricación, se recomienda sólo utilizar tolerancias específicas en áreas realmente críticas.
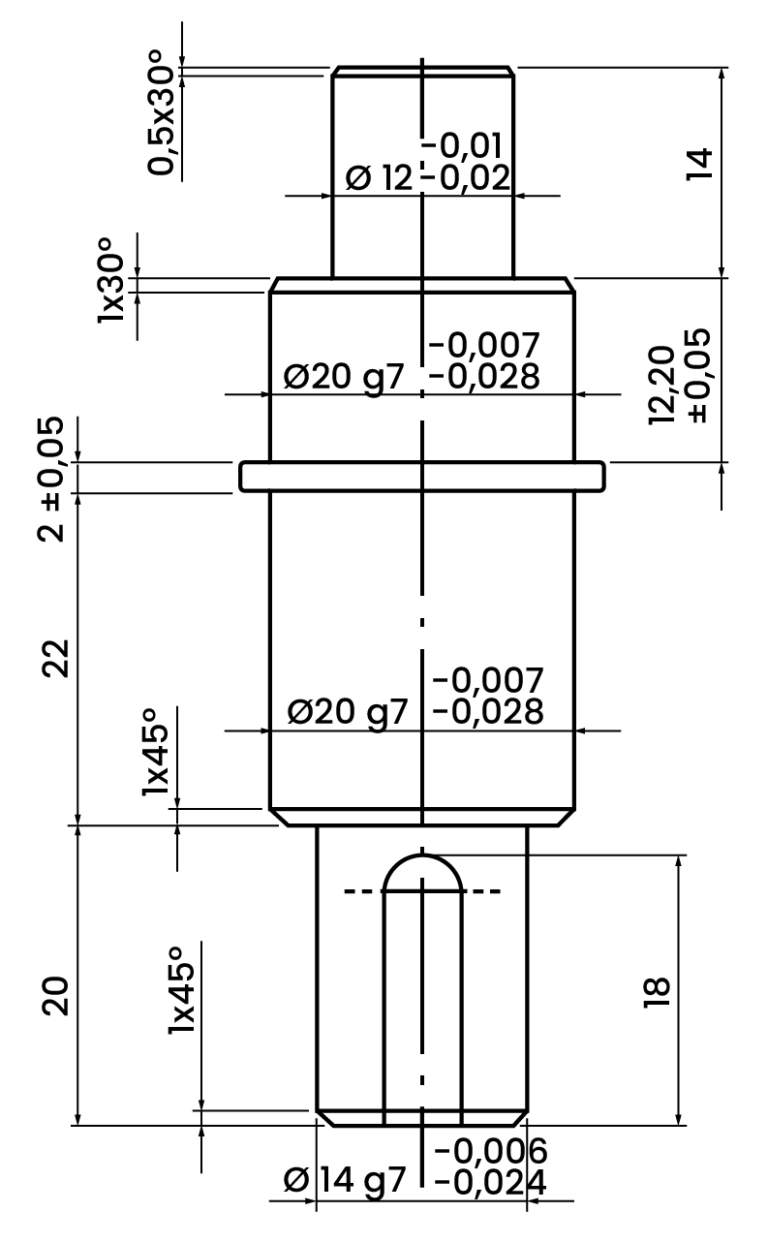
Restricciones
Proto&Go! sólo puede garantizar tolerancias dimensionales superiores a IT7 (H7, g8, P9,….) así como rugosidades superficiales superiores a Ra 1,6.
Valores más restrictivos requieren procesos de rectificado posteriores al mecanizado CNC.
Si tiene preguntas adicionales, siempre puede ponerse en contacto con el departamento de Atención al Cliente de Proto&Go! en:
info@protoandgo.com | (+34) 932 20 71 04
o a través de nuestro sistema de chat online.