Guide de Design
- Impression 3D -
PRINCIPES DE L’IMPRESSION 3D
Par impression 3D, nous entendons les processus à partir desquels la construction physique d’un design 3D peut être réalisée à travers la technique de fabrication additive.
Au contraire de l’usinage CNC, où la pièce est obtenue par la soustraction de matière d’un bloc initial, dans la fabrication additive, la géométrie est obtenue par la solidification couche par couche de la matière initiale.
Traditionnellement, cette technique est plus courante et utilisée pour les matériaux plastiques, bien que le métal et d’autres matériaux fassent progressivement leur apparition.
AVANTAGES DE L’IMPRESSION 3D
Délais de livraison rapides
Les pièces sont généralement expédiées en 5 jours, ce qui permet d’accélérer les itérations de design et la rapidité de mise sur le marché.
Géométries complexes
Pratiquement n’importe quelle géométrie, même la plus complexe, peut être construite sans les limitations d’autres systèmes de production.
Coût
Cette technologie étant facile à mettre en œuvre, le coût de production des pièces est généralement inférieur à celui de toute autre technologie, ce qui en fait le choix idéal pour le préprototypage et les tests rapides de produits.
Scalabilité
Avec l’impression 3D Proto&Go! une seule pièce peut être produit aussi facilement que des dizaines de pièces de production, sans qu’il soit nécessaire d’investir dans des outillage ou des moules.
Durabilité
L’impression 3D peut offrir une résistance élevée aux chocs, une flexibilité moyenne et une grande résistance aux facteurs environnementaux.
AVANTAGES DE L’IMPRESSION 3D
MJF – Multijet Fusion de HP
Il s’agit de la technologie d’impression de qualité industrielle la plus récente et la plus avancée. C’est pour cette raison que le MTF a été choisi par Proto&Go! pour la réalisation de vos projets.
Cette machine a été mise au point par la société HP pour obtenir tant des prototypes que des séries de pièces dans des matériaux tels que le Nylon – PA12 – ou le TPU flexible, entre autres.
Il faut souligner la rapidité de fabrication et la résistance des pièces obtenues, car on peut obtenir des pièces 100 % fonctionnelles en quelques jours et avec une haute résolution.
SLS – Selective Laser Sintering
La stéréolithographie appartient à une famille de technologies de fabrication additive connue sous le nom de photopolymérisation ou, plus communément, d’impression 3D en résine. Le principe de cette technique est l’utilisation d’une source lumineuse (un laser) pour durcir la résine liquide et la transformer en plastique rigide.
Les pièces fabriquées à l’aide de la technologie SLA offrent la résolution et la précision les plus élevées, les détails les plus nets et la finition de surface la plus lisse de toutes les technologies d’impression 3D et sont idéales pour les pièces esthétiques.
En revanche, il y a une petite inconvénient : le matériau étant photosensible, les pièces obtenues ne résistent pas au passage du temps ni à l’exposition à la lumière ambiante et sont généralement fragiles pour les sections peu importantes.
Pour cette raison, chez Proto&Go! nous choisissons de préférence l’usinage CNC de l’ABS pour obtenir des pièces à finalité esthétique telles que des boîtiers ou des carénages.
SLS – Selective Laser Sintering
Il s’agit d’une technologie évoluée qui permet d’obtenir des pièces en nylon, en polypropylène ou en d’autres matériaux à partir de la fusion de matériaux pulvérulents en appliquant de la chaleur à l’aide d’un laser à point unique.
La SLS est une technologie antérieure à la MJF qui présente des caractéristiques similaires, mais sans certains de les avantages, tels que l’isotropie des matériaux et le temps de fabrication.
FDM – Fused Deposition Modelling
Cette technique est souvent considérée comme la méthode existante la plus simple La technologie FDM (Fused Deposition Modelling) se compose de 3 éléments principaux : un lit/plaque d’impression sur lequel la pièce est imprimée ; une bobine de filament qui sert de matériau d’impression ; et un extrudeur. En quelques mots, le filament est fondu par l’extrudeuse de l’imprimante 3D, qui dépose le matériau avec précision couche par couche sur le lit d’impression.
Les matériaux les plus courants pour ce type d’impression sont, entre autres, l’ABS et le PLA.
Le grand avantage de cette technique est sa simplicité et son économie, ce qui en fait la technologie la plus courante dans le secteur domestique.
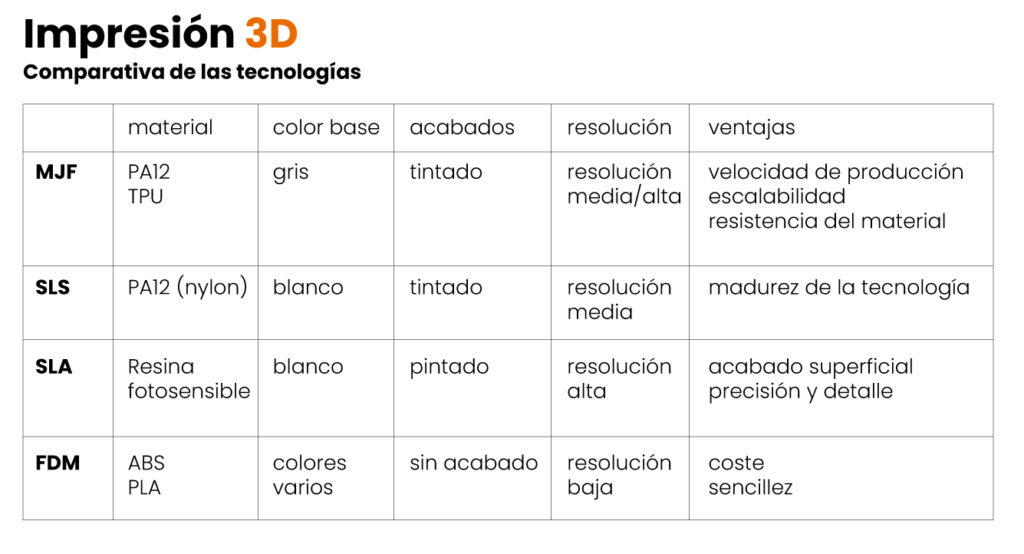
PROCESSUS - MULTIJET FUSION (MJF)
Le processus commence par une tête de revêtement qui dépose une couche très fine (normalement 0,08 mm) du matériau en poudre, PA12 ou TPU, sur la plate-forme de fabrication. Après le dépôt d’une première couche, une seconde tête mobile applique sur la géométrie de la pièce les agents qui délimiteront la zone à sintériser par un fusor qui intègre la tête.
Lorsque toute la section transversale a été scannée, la plate-forme de construction, descend une épaisseur de couche en hauteur. La poudre non sintérisée reste en place pour soutenir les couches suivantes, ce qui élimine le besoin de structures de soutien.
La tête de revêtement dépose une nouvelle couche de poudre sur la couche précédente, déjà sintérisée et la tête avec les agents et le fusor effectue un nouveau passage pour sintériser la nouvelle section sur les sections précédemment solidifiées. Ce processus est répété jusqu’à ce que toutes les pièces soient complètement fabriquées.
Le résultat est un récipient rempli de poudre et de pièces solidifiées qu’il faut laisser refroidir pendant 24 heures avant de retirer.
CARACTÉRISTIQUES - MULTIJET FUSION (MJF)
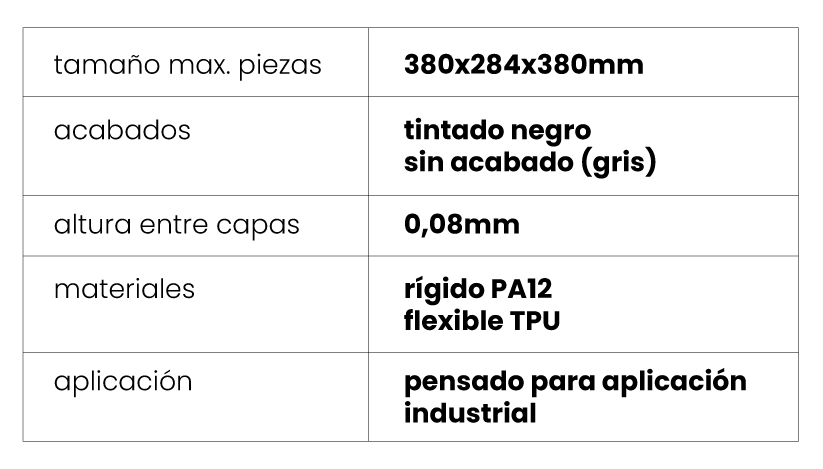
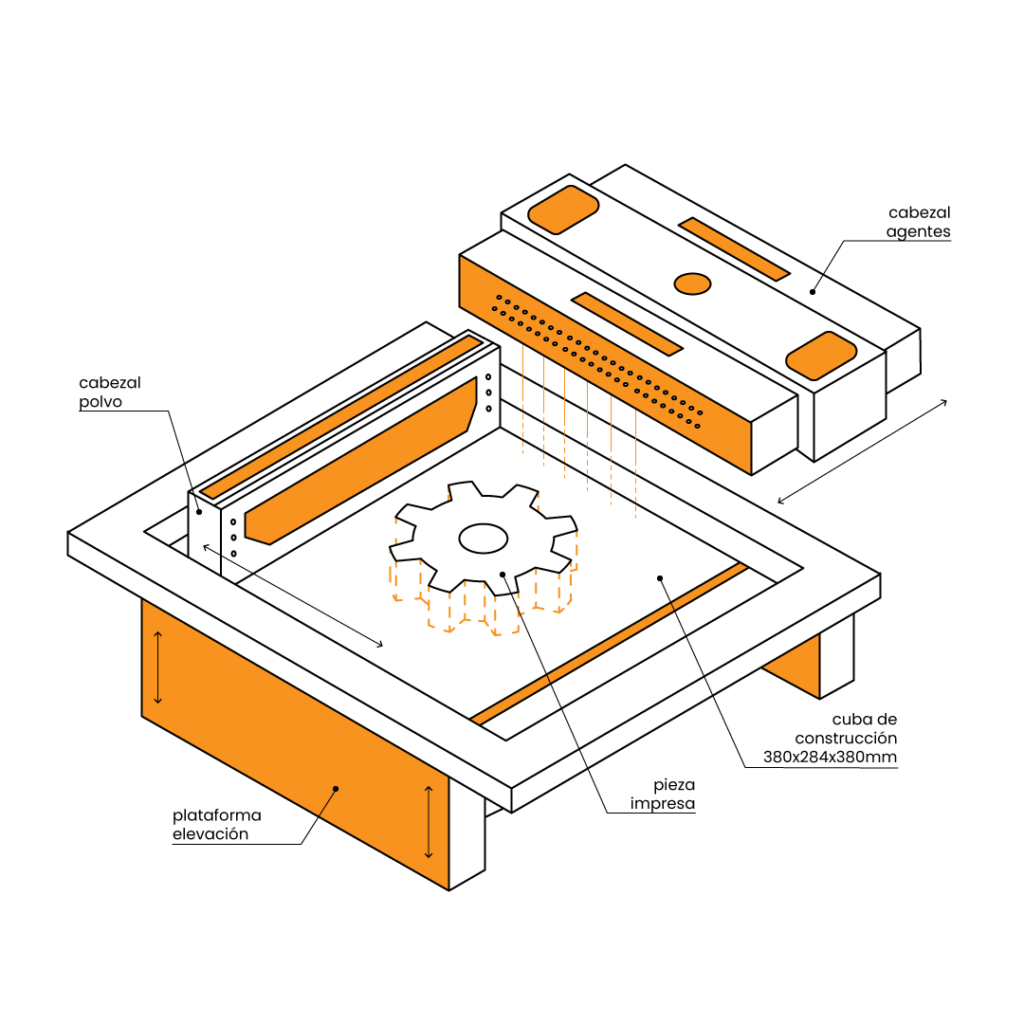
APPLICATIONS- MULTIJET FUSION (MJF)
Les pièces fabriquées par l’impression Multi Jet Fusion sont couramment utilisées au niveau industriel pour la fabrication rapide de prototypes et de séries complètes :
- aérospatiale
- automobile
- produits de consommation
- les produits industriels tels que les machines spéciales
- les soins de santé
Les pièces fonctionnelles et les prototypes MJF sont utilisés pour :
- les drones
- la robotique
- les machines spéciales
- les dispositifs ioT
- les équipements sportifs
- les chaussures
- la technologie orthopédique
- l’éducation
- les dispositifs médicaux
L’impression 3D par MJF est également une excellente technologie pour créer des modèles architecturaux détaillés à un coût raisonnable.
RECOMMANDATIONS DE DESIGN
La plupart des paramètres nécessaires à la stratégie d’impression, comme par exemple la position et l’orientation des pièces dans le récipient sont définis directement par les techniciens de l’impression 3D afin d’optimiser les résultats. En revanche, pendant la phase de développement du produit, les concepteurs et les ingénieurs peuvent également avoir des considérations pour assurer la fabricabilité de la pièce et obtenir des pièces moins chères et plus faciles à fabriquer.
Nous avons regroupé quelques pratiques exemplaires à prendre en compte lors de la conception d’une pièce afin d’en optimiser le coût.
DIMENSIONS
Caractéristiques
L’imprimante Multi Jet Fusion a une taille maximale d’une caisse de 380 x 284 x 380, qui correspond donc à la taille maximale de la pièce pouvant être fabriquée.
Règle du design
- Dimensions maximales des pièces à fabriquer : 380 x 284 x 380 mm.
- Dimensions minimales des pièces à fabriquer : 3 x 3 x 3 x 3 mm.
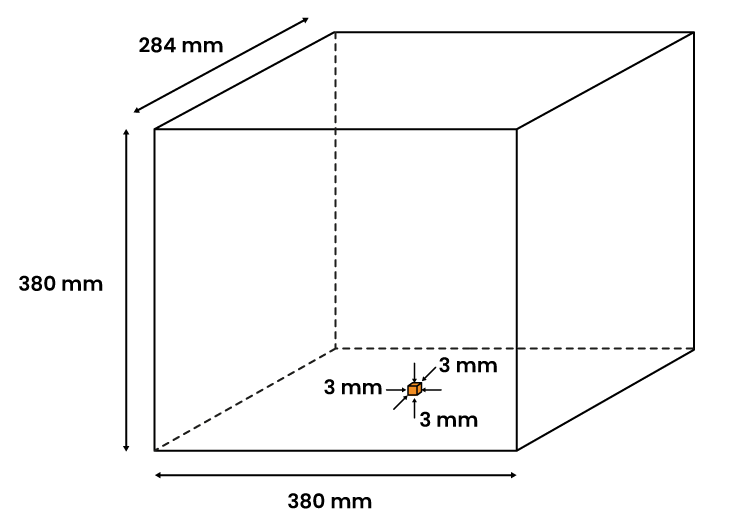
TOLÉRANCES
Caractéristiques
Les tolérances de l’impression 3D, comme celles de tout processus de fabrication, doivent être prises en compte avant d’envisager des ajustements de la conception des pièces.
Règle du design
Tolérance dimensionnelle : ± 0,3% de la taille nominale avec un minimum de ± 0,3 mm.
- Si la dimension est inférieure à 100 mm, la tolérance prévue est de ± 0,3 mm.
- Si la dimension est supérieure à 100 mm, la tolérance prévue est de ± 0,3 % de la dimension originale.
Exemples :
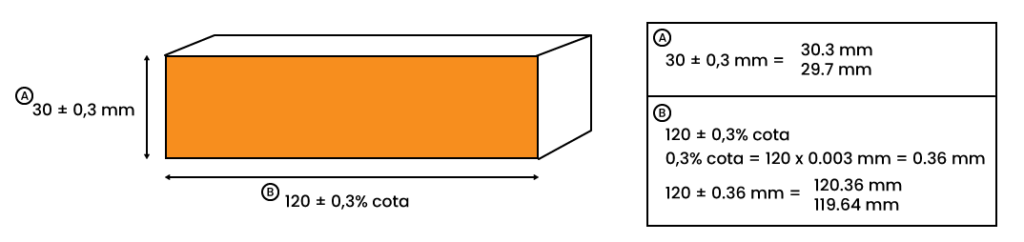
ÉPAISSEUR MINIMALE
Caractéristiques
Les températures élevées générées lors de cette opération peuvent entraîner la déformation ou la rupture des parois trop minces. Il existe donc des valeurs minimales qui ne doivent pas être dépassées afin d’éviter les défaillances de fabrication.
Règle du design
- Épaisseur minimale manufacturable : 0,5 mm.
- Épaisseur minimale recommandée : 0,8 mm
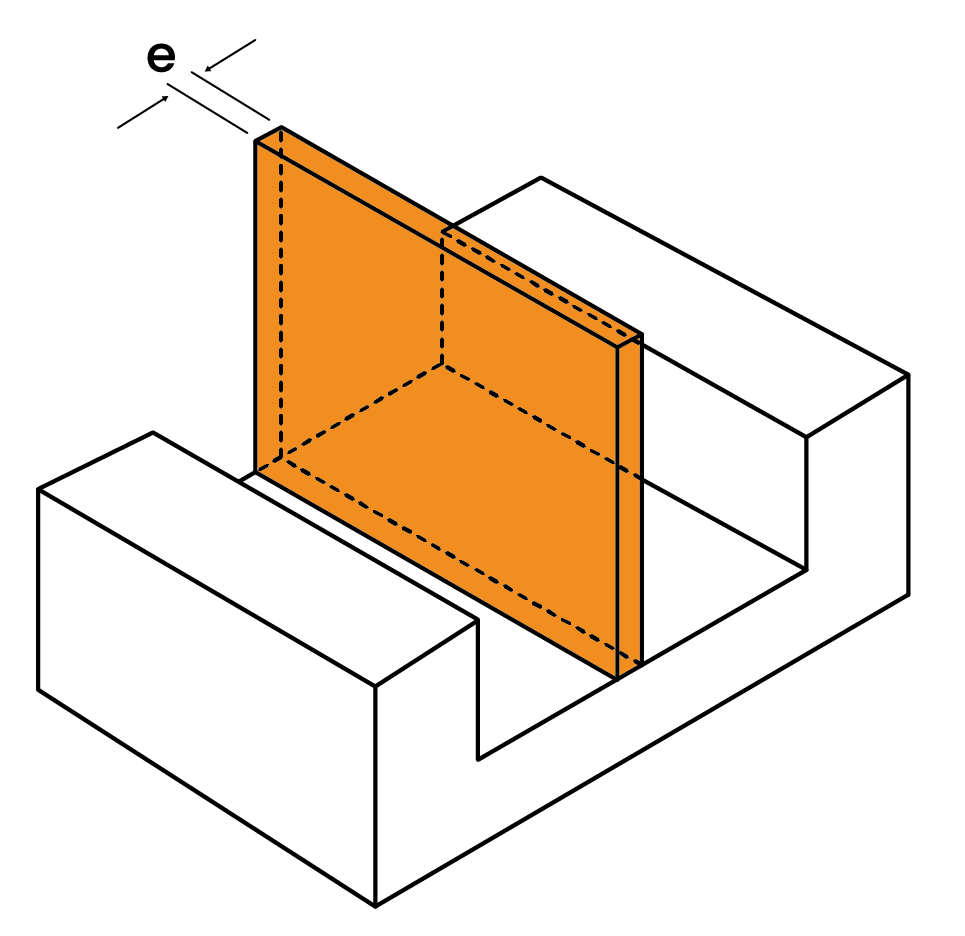
Recommandation
Si des parois affinées (hautes et minces) ou des parois étroites sont nécessaires, il convient de prévoir des nervures ou d’utiliser des parois auxiliaires.
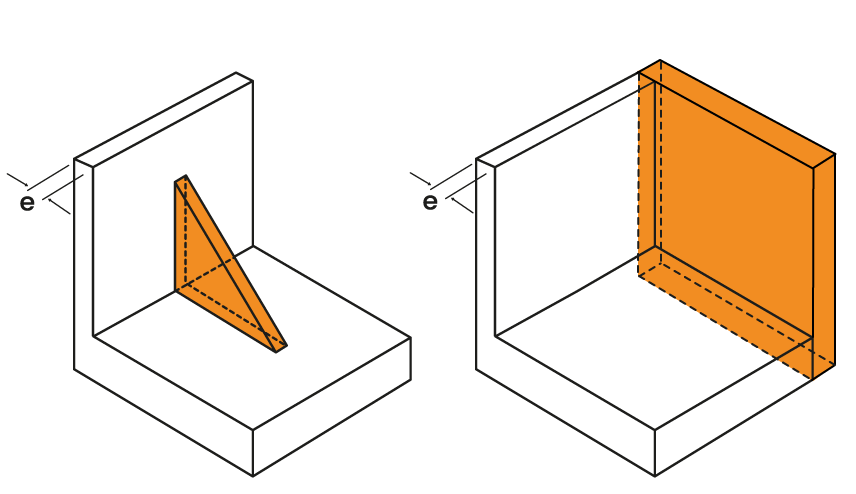
ÉPAISSEUR MAXIMALE
Caractéristiques
La fusion de la poudre à des densités apparentes élevées n’est pas possible en raison de la concentration des températures à l’intérieur de la pièce. En plus, dans le cas de l’impression 3D, le coût principal est donné par la quantité de poudre que contient la pièce.
Pour ces deux raisons, il est recommandé d’éviter les modèles dont l’épaisseur des parois est trop importante.
Règles du design
Épaisseur maximale recommandée :
- Para PA12 – 10 mm.
- Para TPU – 6 mm.
À noter :
Si vous avez besoin d’une épaisseur supérieure à celle recommandée lors de l’impression de la pièce, celle-ci sera automatiquement réalisée avec un « infill » (panneau d’abeille intérieur) avec des parois de 3 mm d’épaisseur et des trous qui permettent la sortie de la poussière logée à l’intérieur. Il est également possible de supprimer la paroi entière et de laisser le panneau d’abeilles visible.
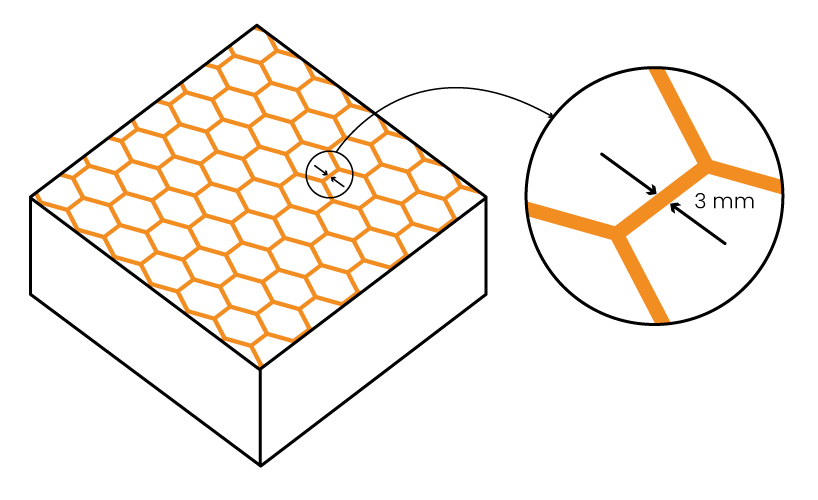
Recommandation
La conception d’une pièce incorpore des éléments structurels qui rigidifient la pièce tout en minimisant les épaisseurs.
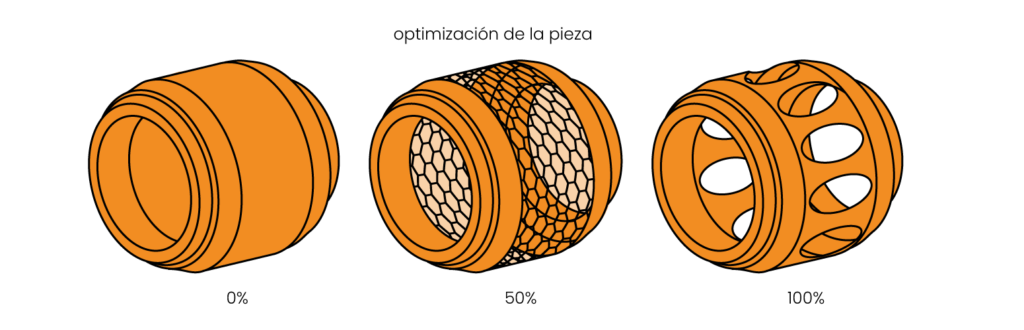
LETTRES OU DESSINS
Caractéristiques
La technologie Multi Jet Fusion vous permet d’imprimer des lettres ou des dessins avec une résolution et une définition très élevée.
Règles du design
- Typographie minimale imprimable : 6 points
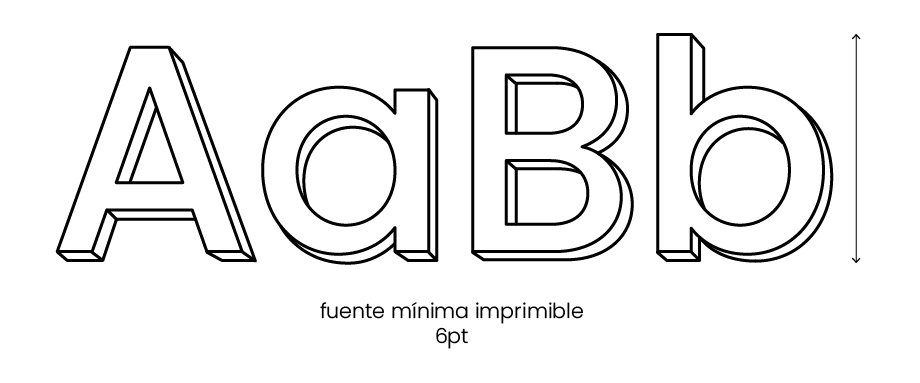
- Hauteur ou profondeur minimale des lettres : 1 mm.
- Largeur minimale des lettres : 0,4 mm.
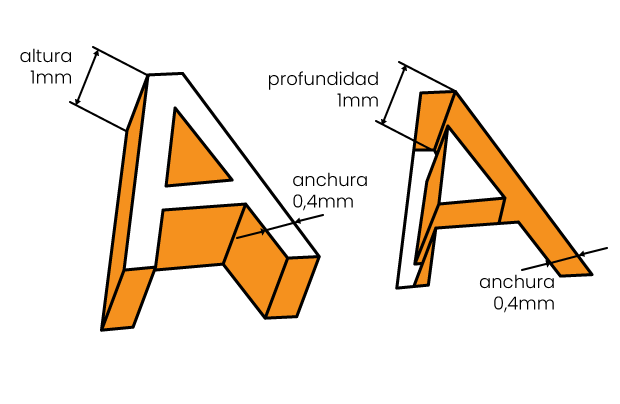
TROUS
Règles du design
- Diamètre minimum recommandé : 1,5 mm.
- Diamètre minimum manufacturable : 0,8 mm.
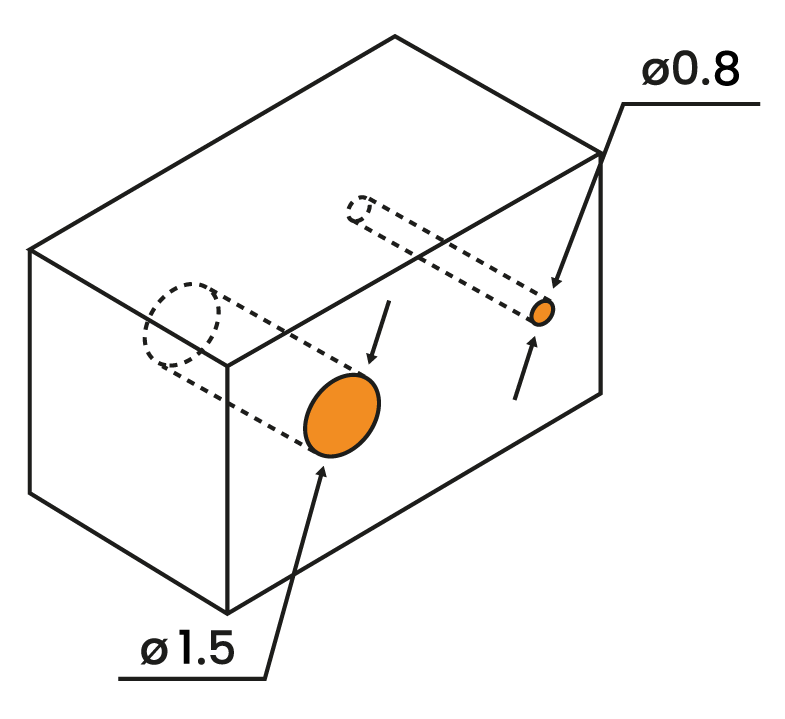
FILETAGES / INSERTS
Caractéristiques
Les filetages d’un diamètre supérieur à M5 sont imprimables dans les deux formats, c’est-à-dire mâle et femelle et sont fonctionnels grâce à la technologie Multi Jet Fusion.
Les inserts métalliques sont également disponibles.
Recommandation
Pour éviter les problèmes de filetage, il est recommandé de concevoir les taraudages avec une tolérance de 0,2 mm de diamètre.
De cette façon, si vous souhaitez obtenir un arbre fileté de M6, dont le diamètre extérieur réglementaire devrait être de Ø6, notre recommandation est de réduire ce diamètre extérieur à Ø5,8 pour éviter les problèmes de tolérance lors du filetage.
Dans le cas d’un trou fileté, d’un écrou ou d’une femelle, la tolérance doit être positive, ce qui rend le diamètre plus grand qu’il ne devrait l’être à l’origine.
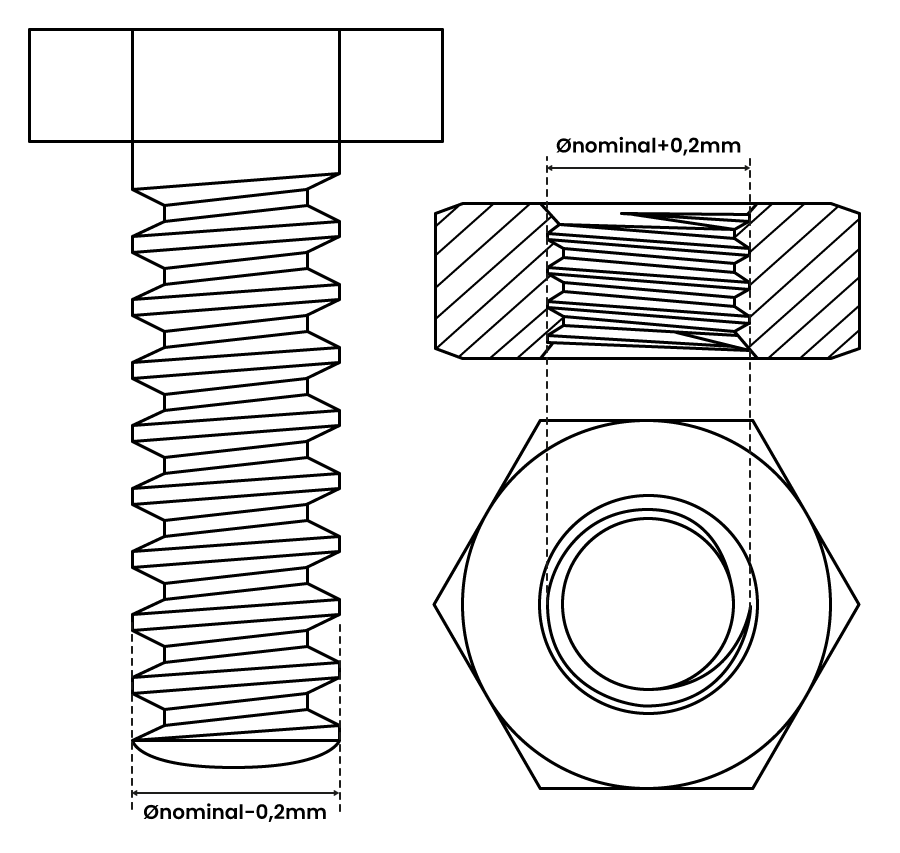
- Vis : Øextérieur = Ønominal – 0,2 mm.
- Écrou : Øintérieur = Ønominal + 0,2 mm.
À noter :
Pour les filetages de M3 à M8, les inserts métalliques sont la meilleure solution pour l’exécution de filetages dans une pièce imprimée.
Si vous avez des questions, vous pouvez contacter le service client de Proto&Go! à
info@protoandgo.com | (+33) 176 44 09 62
ou sur notre chat online.