Guida al Design
- Stampa 3D -
PRINCIPI DELLA STAMPA 3D
Per stampa 3D si intendono i processi da cui si può ottenere la costruzione fisica di un design 3D attraverso la tecnica della fabbricazione additiva.
A differenza della lavorazione CNC, nella quale il pezzo è ottenuto sottraendo materiale da un blocco iniziale, nella fabbricazione additiva la geometria è ottenuta solidificando il materiale iniziale strato per strato.
Tradizionalmente, questa tecnica è più comune e utilizzata per i materiali plastici, anche se il metallo e altri materiali stanno gradualmente emergendo.
VANTAGGI DELLA STAMPA 3D
Tempi di consegna veloci
I componenti sono tipicamente spediti entro 5 giorni, che permette iterazioni di progettazione e velocità di commercializzazione più rapide.
Geometrie complesse
Praticamente qualsiasi geometria, anche la più complessa, può essere costruita senza le limitazioni di altri sistemi di produzione.
Costo
Essendo una tecnologia alta e facile da produrre, i costi per ottenere pezzi sono generalmente più bassi di qualsiasi altra tecnologia, essendo la scelta ideale per pre-prototipi e test rapidi del prodotto.
Scalabilità
Con la stampa 3D da Proto&Go! un singolo pezzo può essere prodotto con la stessa facilità con cui si producono decine di pezzi di produzione, senza la necessità di investire in attrezzature o stampi.
Durabilità
La stampa 3D può offrire un’alta resistenza agli impatti, una media flessibilità e un’alta resistenza ai fattori ambientali.
TECNOLOGIE DI STAMPA 3D
MJF – Multi Jet Fusion by HP
Questa è l’ultima e più avanzata tecnologia di stampa di qualità industriale. Ecco perché Proto&Go! ha scelto la MTF per la realizzazione dei tuoi progetti.
Questa macchina è stata sviluppata da HP per produrre sia prototipi che serie di pezzi in materiali come il Nylon – PA12 – o il TPU flessibile, per citarne alcuni.
La velocità di fabbricazione e la resistenza dei pezzi ottenuti sono particolarmente degne di nota, dato che i pezzi funzionali al 100% possono essere ottenuti in pochi giorni e con un’alta risoluzione.
SLA – Stereolitografia
La stereolitografia appartiene a una famiglia di tecnologie di fabbricazione additiva conosciuta come fotopolimerizzazione o comunemente, stampa 3D in resina. Questa tecnica utilizza una fonte di luce (un laser) per polimerizzare la resina liquida in una plastica solida.
I componenti realizzati mediante SLA offrono la più alta risoluzione e precisione, i dettagli più nitidi e la finitura superficiale più liscia di tutte le tecnologie di stampa 3D, rendendola ideale per pezzi estetici.
D’altra parte, hanno uno svantaggio, cioè che il materiale è fotosensibile, quindi i pezzi ottenuti non sono resistenti al trascorrere del tempo o all’esposizione alla luce ambientale e sono generalmente fragili per sezioni di altezza non molto elevata.
Per questo motivo, in Proto&Go! preferiamo optare per la lavorazione CNC dell’ABS per ottenere pezzi con obiettivi estetici come alloggiamenti o carenature.
SLS – Sinterizzazione laser selettiva
Si tratta di una tecnologia consolidata che permette la produzione di componenti in nylon, polipropilene o altri materiali dalla fusione di materiali in polvere applicando il calore con un unico punto laser.
SLS è una tecnologia pre-MJF con caratteristiche simili, ma senza alcuni dei suoi vantaggi, come l’isotropia del materiale e il tempo di fabbricazione.
FDM – Modellazione a deposizione fusa
Questa tecnica è spesso considerata il metodo più semplice esistente. La tecnologia FDM (Fused Deposition Modelling) consiste in 3 elementi principali: un letto/piastra di stampa su cui viene stampato il pezzo; una bobina di filamento che serve come materiale di stampa; e un estrusore. In poche parole, il filamento viene fuso dall’estrusore della stampante 3D, che deposita il materiale con precisione strato per strato sul letto di stampa.
I materiali più comuni per questo tipo di stampa sono ABS e PLA.
Il grande vantaggio di questa tecnica è la sua semplicità ed economia, che la rende la tecnologia più comune nel settore domestico.
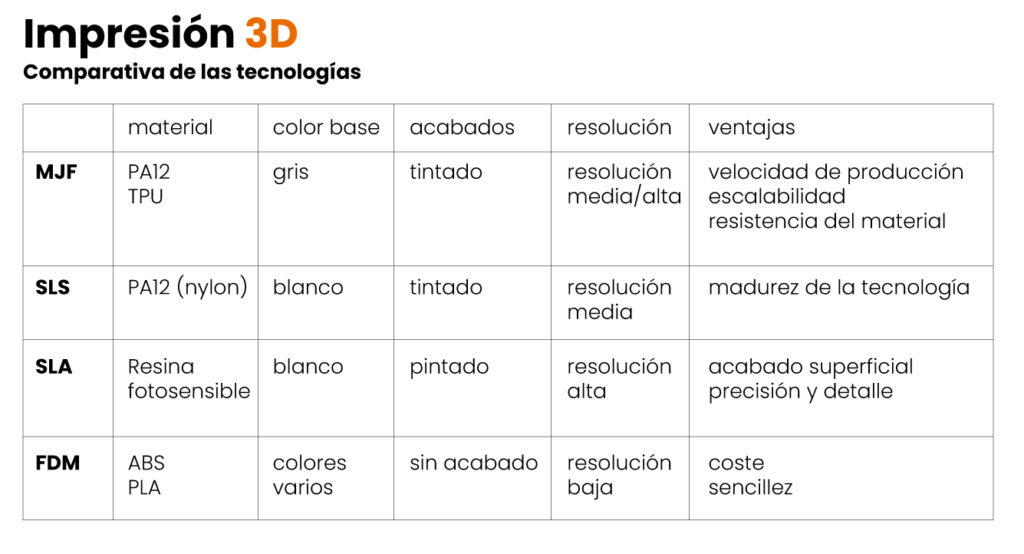
PROCESSO - FUSIONE A GETTO MULTIPLO (MJF)
Il processo inizia con una testa di rivestimento che deposita uno strato molto sottile (normalmente 0,08 mm) del materiale in polvere, PA12 o TPU, sulla piattaforma di costruzione. Dopo che il primo strato è stato depositato, una seconda testa mobile applica degli agenti alla geometria del pezzo che delimiterà l’area da sinterizzare tramite un fusore che integra la testa.
Quando l’intera sezione trasversale è stata scansionata, la piattaforma di costruzione abbassa uno spessore di strato in altezza. La polvere non sinterizzata rimane sul posto per sostenere gli strati successivi, eliminando la necessità di strutture di supporto.
La testa di rivestimento deposita un nuovo strato di polvere sopra il precedente strato già sinterizzato e la testa con gli agenti e il fusore fa un nuovo passaggio per sinterizzare la nuova sezione sulle sezioni precedentemente solidificate. Questo processo si ripete fino a quando tutte i cmponenti sono completamente fabbricati.
Il risultato è un contenitore pieno di polvere e pezzi solidificati che devono essere lasciati raffreddare per 24 ore prima di essere rimossi.
CARATTERISTICHE - MULTI JET FUSION (MJF)
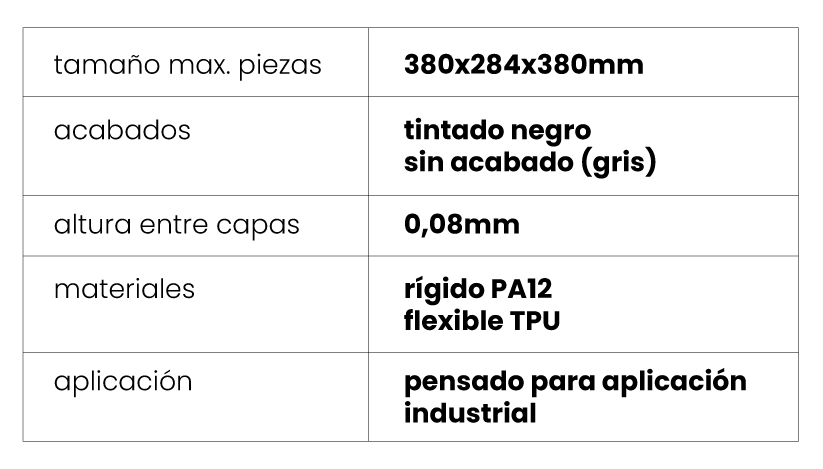
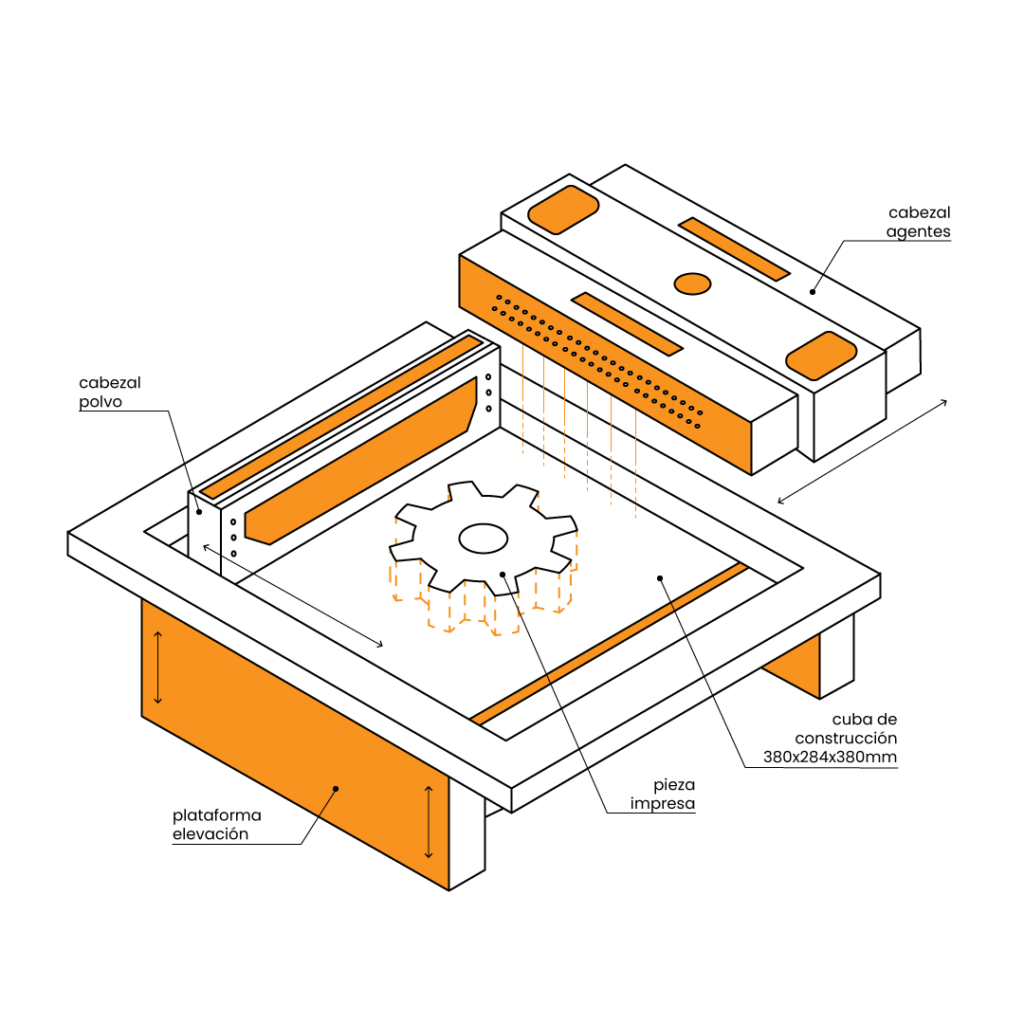
APPLICAZIONI - MULTI JET FUSION (MJF)
I componenti prodotti con la stampa Multi Jet Fusion sono comunemente utilizzati a livello industriale per prototipi rapidi e serie complete:
- aerospaziale
- automobilistico
- prodotti di consumo
- prodotti industriali come macchinari speciali
- sanità
I pezzi funzionali e i prototipi MFJ sono utilizzati per:
- droni
- robotica
- macchine speciali
- dispositivi ioT
- equipaggiamento sportivo
- calzature
- tecnologia ortopedica
- istruzione
- dispositivi medici
La stampa 3D MFJ è anche una tecnologia eccellente per creare modelli architettonici dettagliati a un costo ragionevole.
RACCOMANDAZIONI PER IL DESIGN
La maggior parte dei parametri necessari per la strategia di stampa, come la posizione e l’orientamento dei pezzi nel contenitore, sono impostati direttamente dai tecnici della stampa 3D per ottimizzare i risultati. D’altra parte, durante la fase di sviluppo del prodotto, i progettisti e gli ingegneri possono anche avere considerazioni per assicurare la fabbricabilità del componente e ottenere pezzi più economici e facili da produrre.
Abbiamo messo insieme alcune buone pratiche da considerare quando si progetta un componente per ottimizzarne il costo.
DIMENSIONI
Caratteristiche
La stampante Multi Jet Fusion ha una dimensione massima del serbatoio di 380 x 284 x 380, che è la dimensione massima del pezzo che può essere prodotto.
Regola del design
- Dimensione massima del pezzo da produrre: 380 x 284 x 380 mm.
- Dimensioni minime dei pezzi da fabbricare: 3 x 3 x 3 x 3 mm.
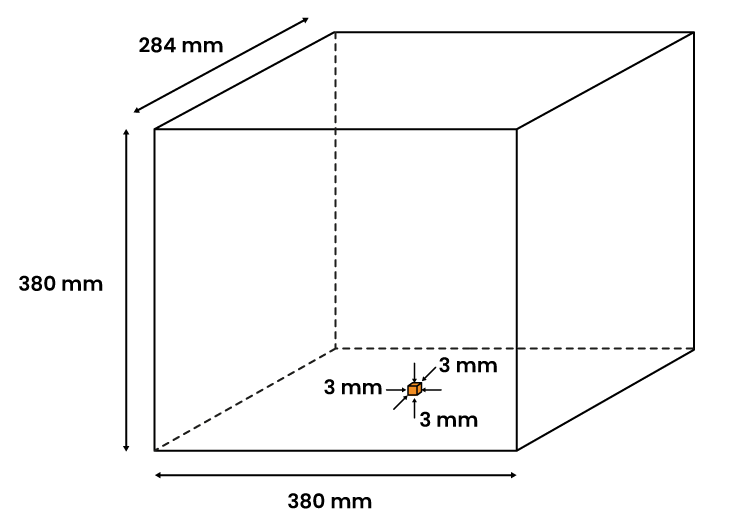
TOLLERANZE
Caratteristiche
Come in ogni processo di fabbricazione, anche nella stampa 3D ci sono alcune tolleranze che devono essere considerate prima di procedere alla progettazione di pezzi che devono essere modificati.
Regola del design
Tolleranza dimensionale: ± 0,3% della dimensione nominale con un minimo di ± 0,3 mm.
- Se la dimensione è inferiore a 100 mm, la tolleranza è di ± 0,3 mm.
- Se la dimensione è superiore a 100 mm, la tolleranza prevista è di ± 0,3%della dimensione originale.
Esempi
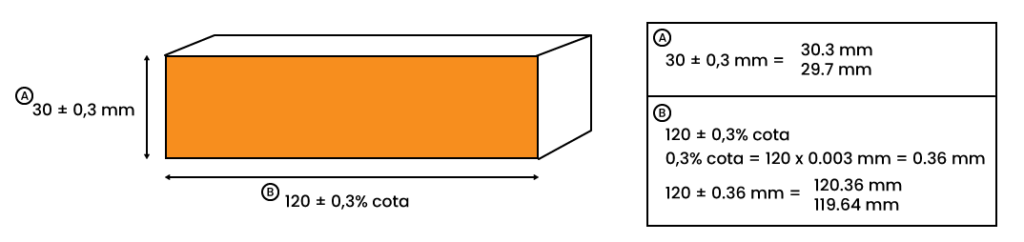
SPESSORE MINIMO
Caratteristiche
Le temperature elevate generate durante la sinterizzazione della polvere possono portare alla deformazione o alla rottura delle pareti sottili. Quindi, ci sono valori minimi che non devono essere superati per evitare difetti di fabbricazione.
Regola del design
- Spessore minimo fabbricabile: 0,5 mm
- Spessore minimo raccomandato: 0,8 mm
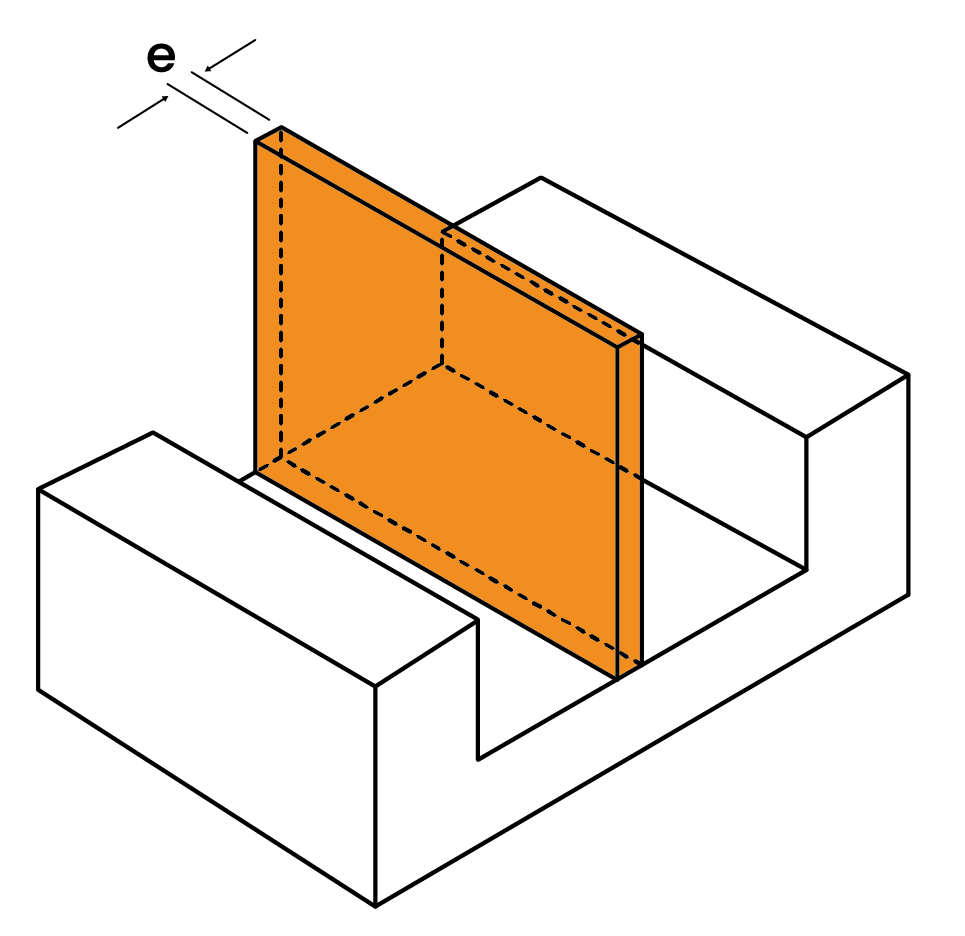
Raccomandazione
Se sono richieste pareti sottili (alte e sottili) o bassi spessori di parete, si raccomanda l’uso di nervature nella parete o di pareti ausiliarie.
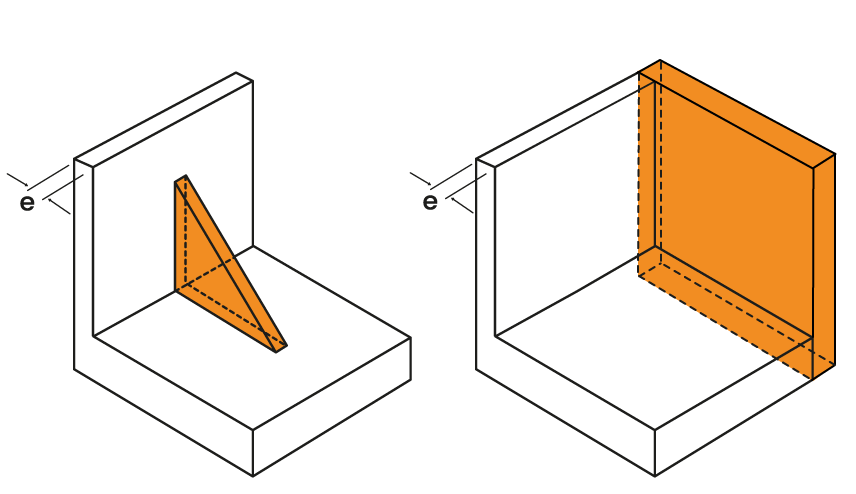
SPESSORE MASSIMO
Caratteristiche
La fusione della polvere ad alte densità di massa non è possibile a causa della concentrazione delle temperature all’interno dei pezzi. Inoltre, nel caso della stampa 3D, il costo principale è dato dalla quantità di polvere che il pezzo contiene.
Per queste due ragioni, si raccomanda di evitare modelli con uno spessore di parete troppo elevato..
Regole del design
Spessore massimo raccomandato:
- PA12 – 10 mm.
- TPU – 6 mm.
Nota:
Se hai bisogno di uno spessore maggiore di quello raccomandato al momento della stampa dei pezzi, questi saranno automaticamente realizzati con un infill (pannello interno/nido d’ape) con pareti spesse 3 mm e fori che permettono alla polvere all’interno di uscire. Si può anche scegliere di rimuovere l’intera parete e lasciare il pannello dell’ape visibile.
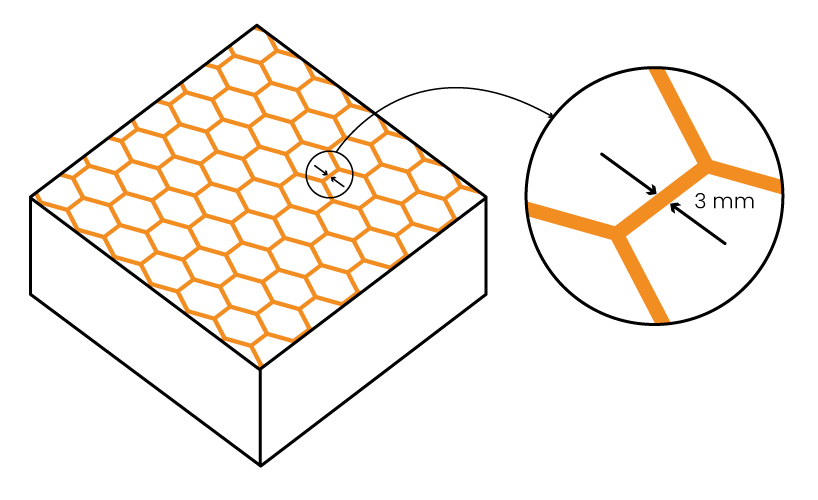
Raccomandazione
Progettare un componente che abbia elementi strutturali in grado di irrigidire il pezzo minimizzando lo spessore.
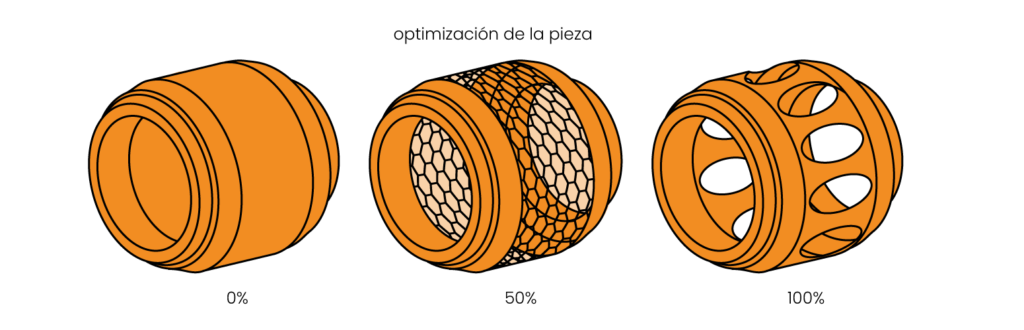
LETTERE O DISEGNI
Caratteristiche
La tecnologia Multi Jet Fusion permette di stampare lettere e/o disegni ad altissima risoluzione e definizione.
Regole del design
- Tipo minimo stampabile: 6 punti
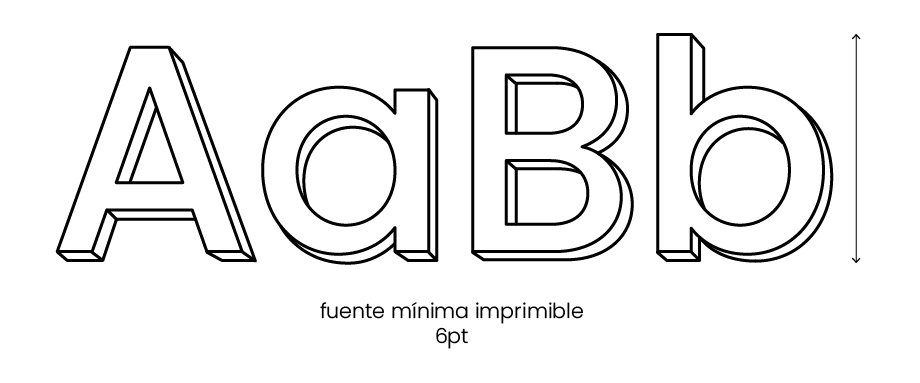
- Altezza o profondità minima delle lettere: 1 mm.
- Larghezza minima delle lettere: 0,4 mm.
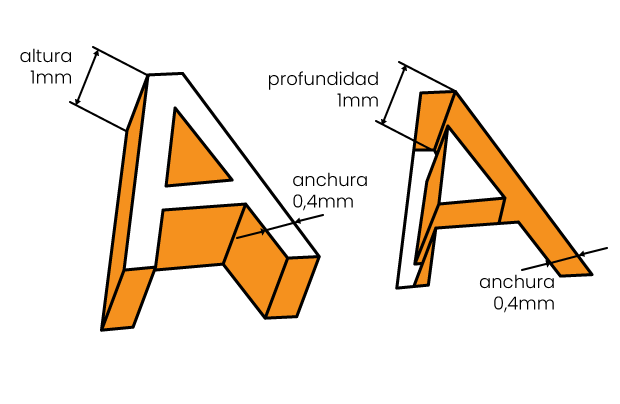
FORI
Regole del design
- Diametro minimo raccomandato: 1,5 mm
- Diametro minimo fabbricabile: 0,8 mm
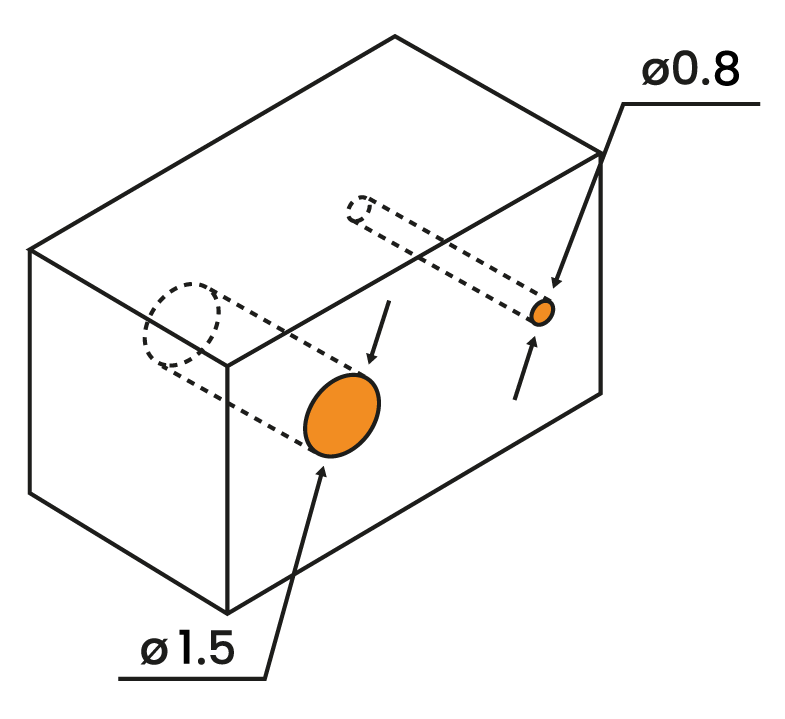
FILETTATURE/INSERTI
Caratteristiche
Le filettature più grandi di M5 sono stampabili in entrambi i formati maschio e femmina e sono funzionali alla tecnologia Multi Jet Fusion.
Sono possibili anche inserti di metallo.
Raccomandazione
Per evitare problemi di filettatura, si raccomanda di progettare le filettature con una tolleranza di 0,2 mm di diametro.
Così, se si vuole ottenere un albero filettato M6, che dovrebbe avere un diametro esterno di Ø6, Così, se si vuole ottenere un albero filettato M6, che dovrebbe avere un diametro esterno di Ø5,8 per evitare problemi di tolleranza durante la filettatura.
Nel caso di un foro filettato, dado o femmina, la tolleranza deve essere positiva, rendendo il diametro maggiore di quello che dovrebbe essere in origine.
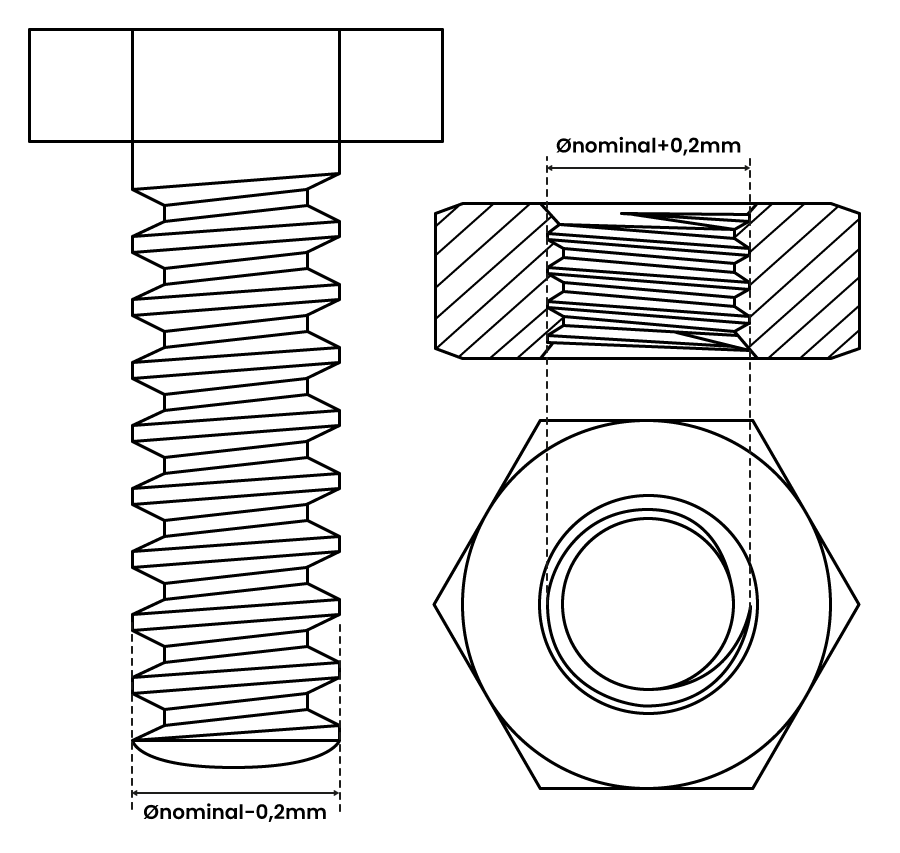
- Bullone: Øesterno = Ønominale – 0,2 mm.
- Dado: Øinterno = Ønominale + 0,2 mm.
Nota:
Per le filettature da M3 a M8, gli inserti metallici sono la soluzione migliore per fare le filettature in un pezzo stampato.
Se hai delle domande, puoi contattare il servizio clienti di Proto&Go! a
info@protoandgo.com | (+39) 011 1962 0263
Se preferisci nella nostra chat online.